Production Process
World-Class
Plastic Injection Mould Tooling
World-Class Plastic Injection Mould Tooling, Tool Design, End of Arm Tooling, Gauges and Checking Fixtures Production Process at HH Plastic Metal Co., Ltd.
At HH Plastic Metal Co., Ltd, we are committed to delivering world-class plastic injection mould tools for our Tier 1 and OEM clients. Our comprehensive production process ensures the highest quality, precision, and performance in every tool we manufacture. Here’s an in-depth look at our meticulously crafted production process:
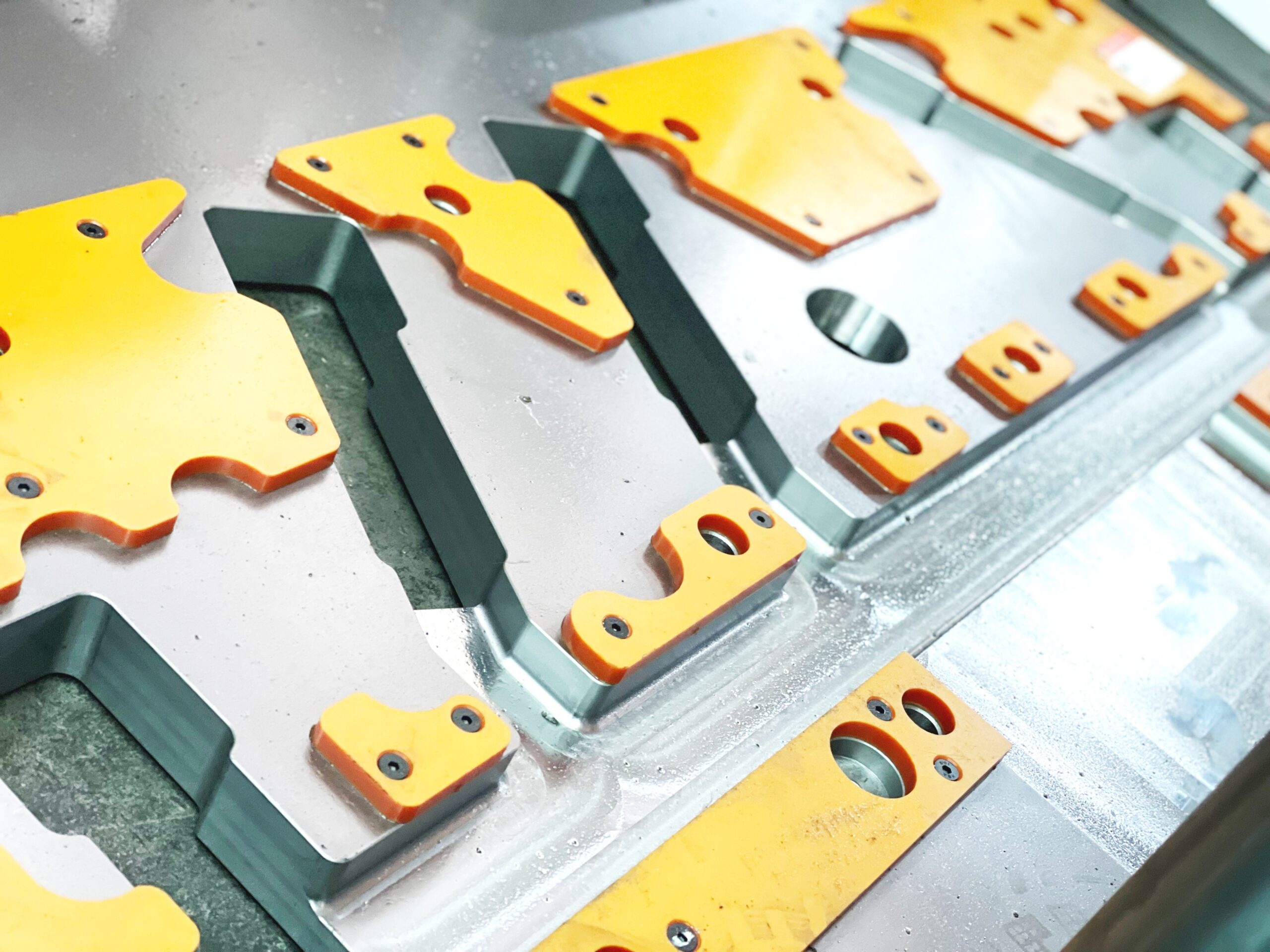
we are committed to providing exceptional customer service and maintaining transparent communication
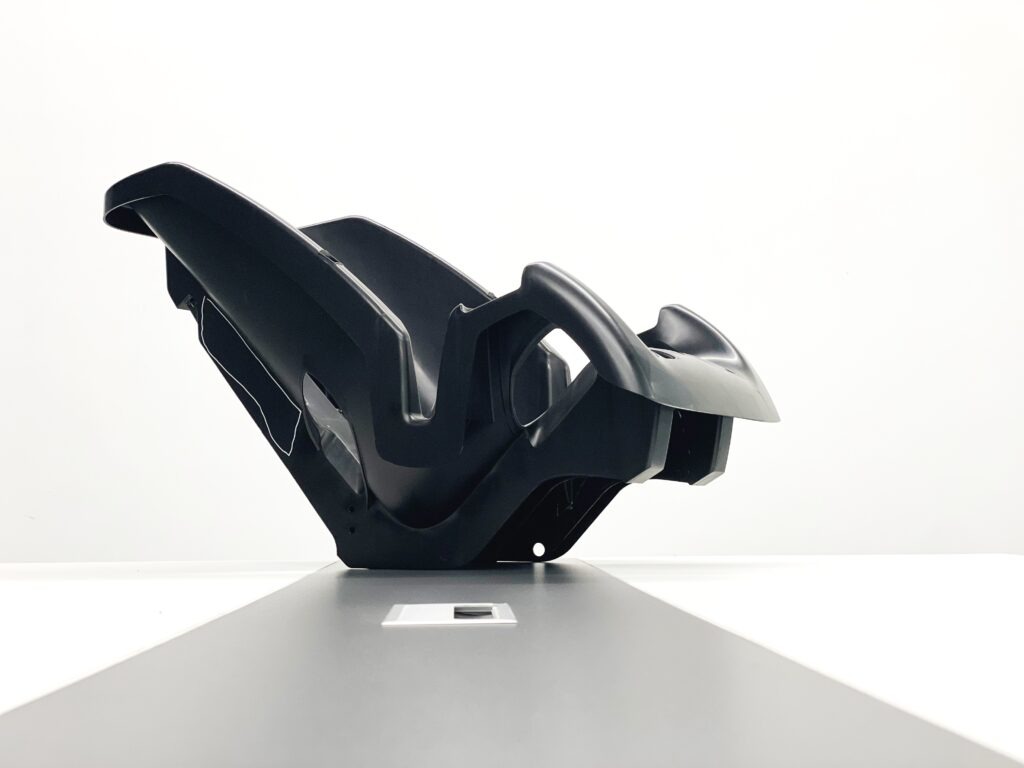
- Design for Manufacturability (DFM) is the first crucial step in our production process. During DFM, our expert engineers evaluate the client’s design to ensure it can be efficiently and cost-effectively manufactured. This process involves:
- Detailed Analysis: Assessing the design for potential issues that could arise during manufacturing.
- Optimisation: Making necessary adjustments to improve manufacturability while maintaining the design’s integrity and functionality.
- Feedback: Providing detailed feedback to the client to ensure all design aspects are aligned with manufacturing capabilities.
- Moldflow Analysis is essential for predicting how the plastic material will flow during the injection process. This step includes:
- Simulation: Using advanced software to simulate the injection moulding process.
- Optimisation: Identifying potential defects such as warping, air traps, and sink marks, and optimising the design to minimize these issues.
- Validation: Ensuring that the mould design supports efficient production with minimal material waste and cycle times.
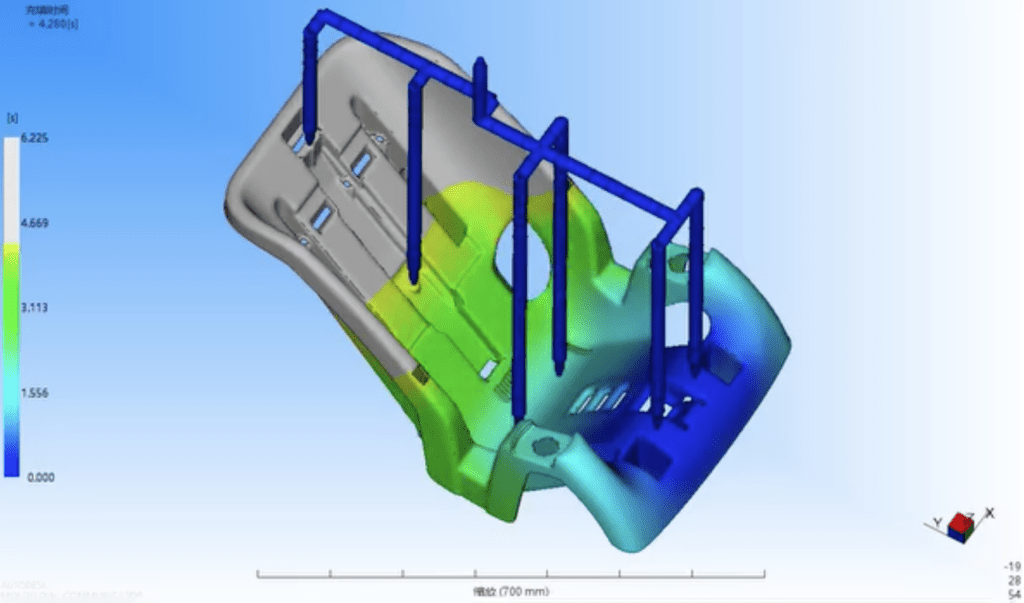
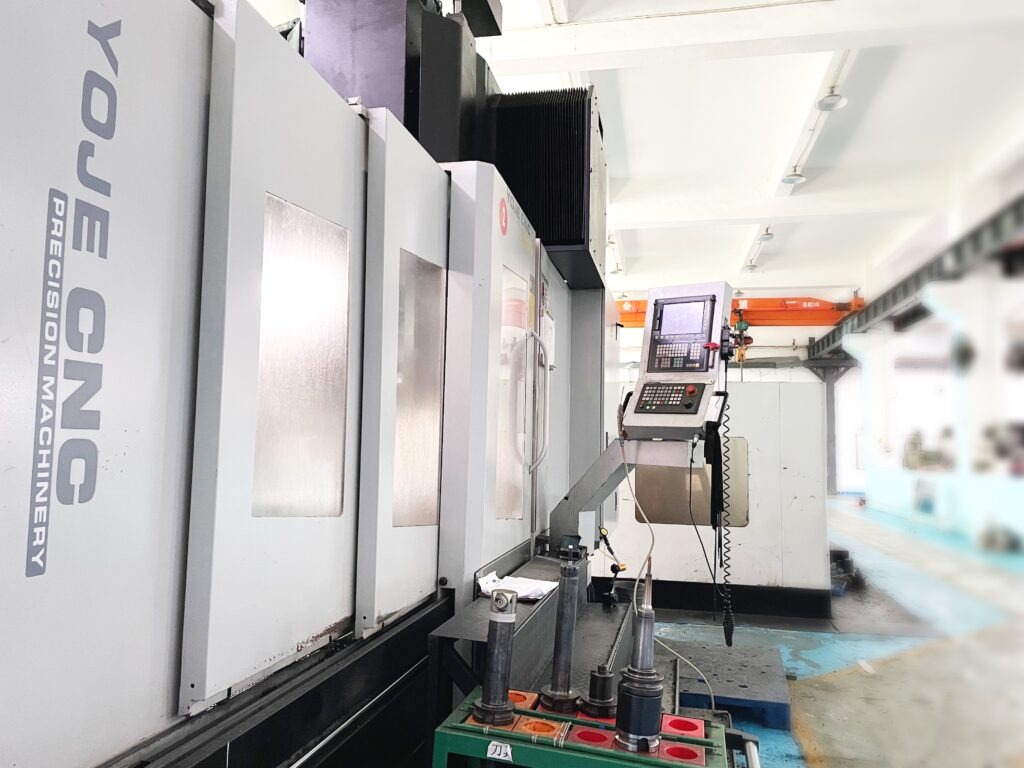
- Our Tool Design phase focuses on creating detailed plans for the injection mould tool. This phase involves:
- CAD Modelling: Developing 3D models of the mould tool using cutting-edge CAD software.
- Component Design: Designing each component of the tool, including cores, cavities, runners, and cooling channels.
- Review: Conducting thorough design reviews to ensure all specifications and requirements are met.
- Our online collaboration tools enhance transparency and ensure efficient project management by:
- Document Sharing: Platforms like Google Drive and Dropbox allow for secure, real-time sharing of project documents, designs, and revisions.
- Version Control: Ensuring that all stakeholders have access to the latest versions of documents and designs, preventing confusion and errors.
- Feedback Integration: Facilitating easy incorporation of customer feedback into project designs and plans.
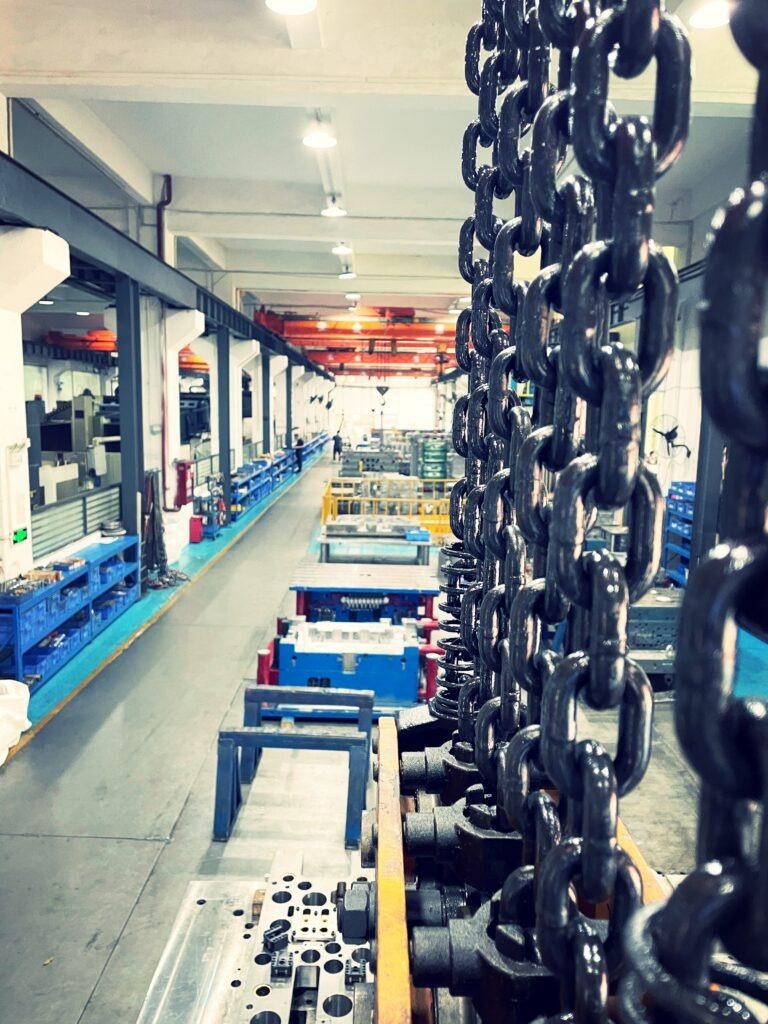
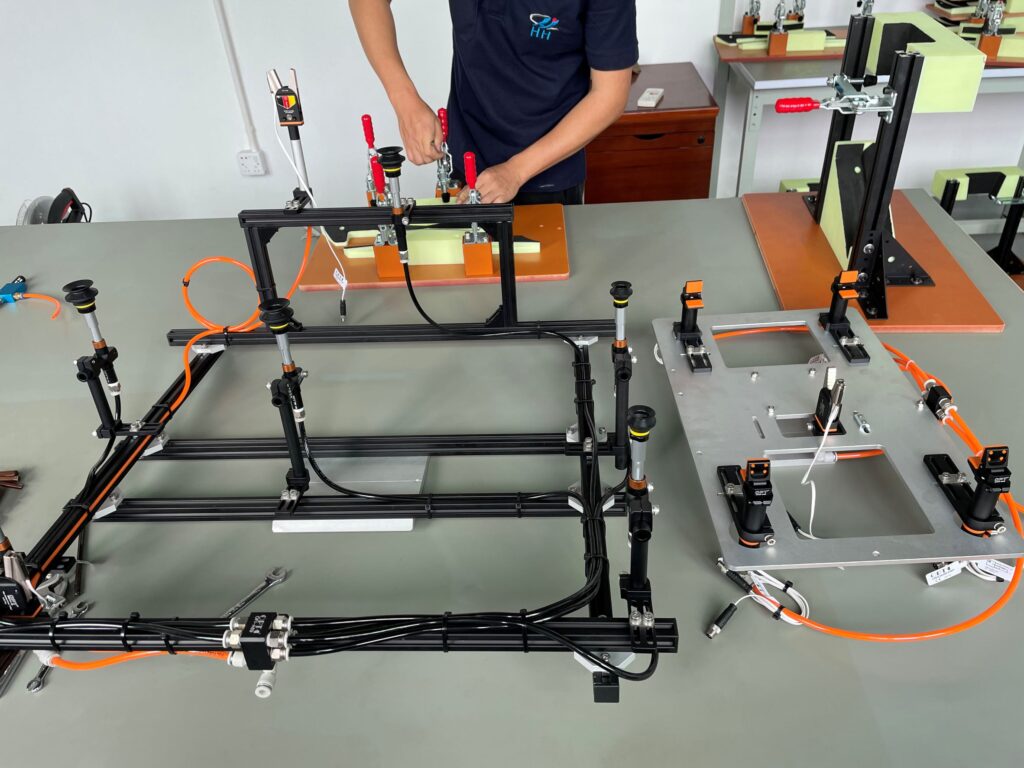
Our capabilities in End Of Arm Tooling enable us to design and produce highly efficient and precise robotic components that enhance automation, streamline operations, and optimise productivity in various manufacturing processes.
Our expertise in Checking Jigs & Fixtures allows us to create custom, precise solutions for accurate measurement and quality control, ensuring that every component meets stringent specifications and industry standards.
Our gauges, utilised in the manufacture of plastic injection moulded components, ensure precise measurements and consistent quality control, enabling us to deliver components that meet exacting standards and performance requirements
- During Tool Trials, we test the mould tool under real production conditions to ensure it performs as expected. This step includes:
- Initial Runs: Conducting initial production runs to identify any issues with the tool.
- Adjustments: Making necessary adjustments to optimise the tool’s performance and quality.
- Validation: Ensuring the tool produces parts that meet all specifications and quality standards.
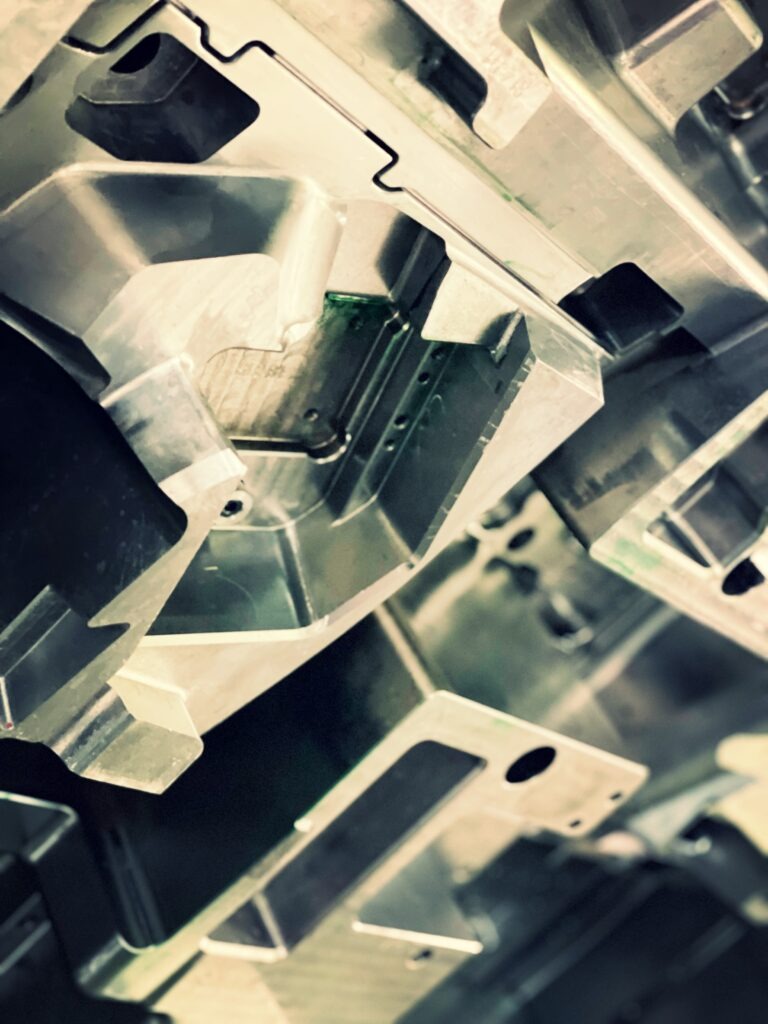
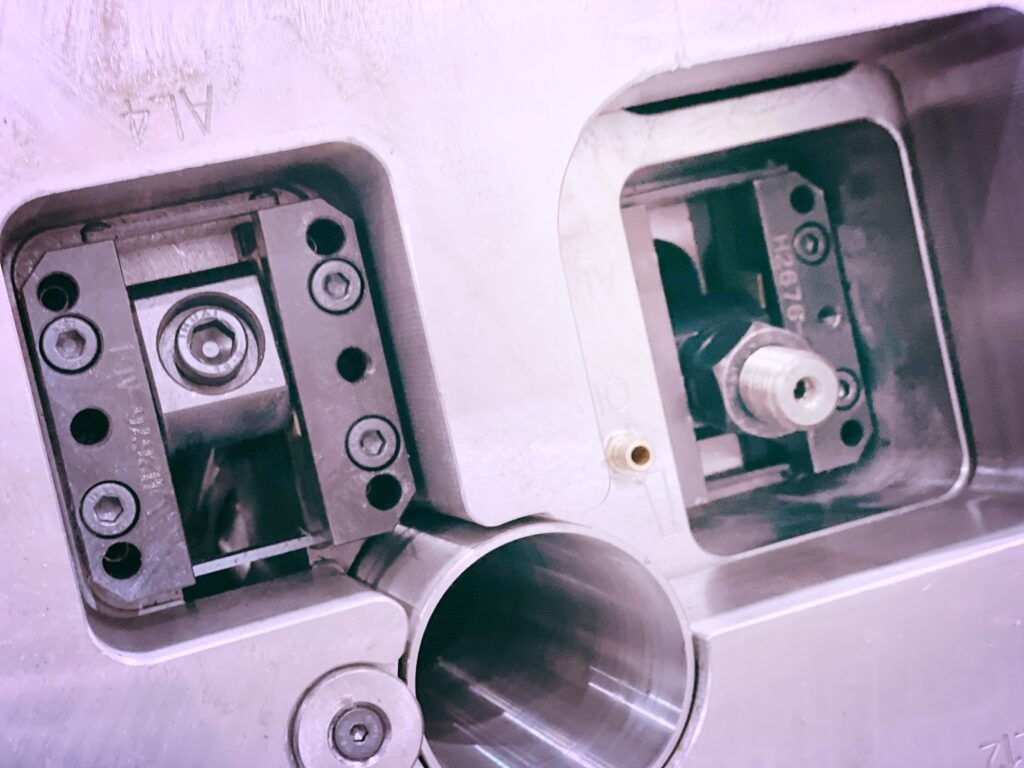
- Product Validation using a Coordinate Measuring Machine (CMM) ensures that the parts produced by the mould tool are dimensionally accurate. This process involves:
- Measurement: Using CMM to measure critical dimensions of the produced parts.
- Comparison: Comparing the measurements to the design specifications.
- Adjustment: Making any required adjustments to the tool to achieve precise part dimensions.
- Tool Validation and Approval is the final step before shipping the tool to the client. This phase includes:
- Final Testing: Conducting comprehensive tests to confirm the tool’s performance and durability.
- Approval: Obtaining approval from the client based on the successful validation results.
- Documentation: Providing detailed documentation and reports to the client.
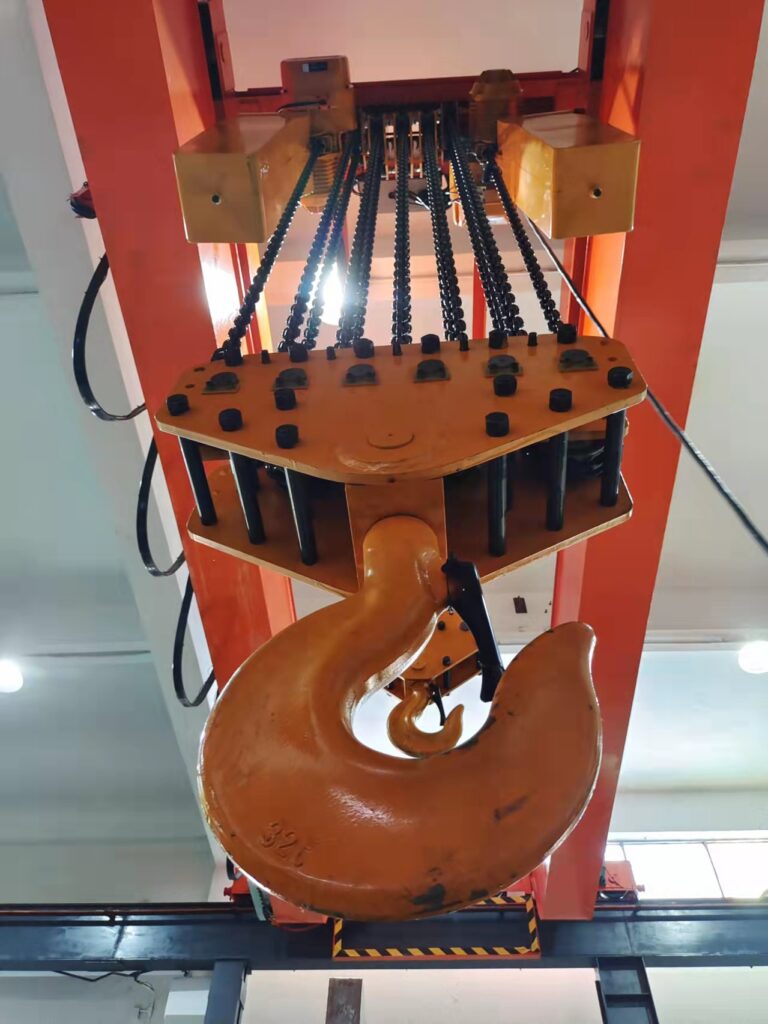
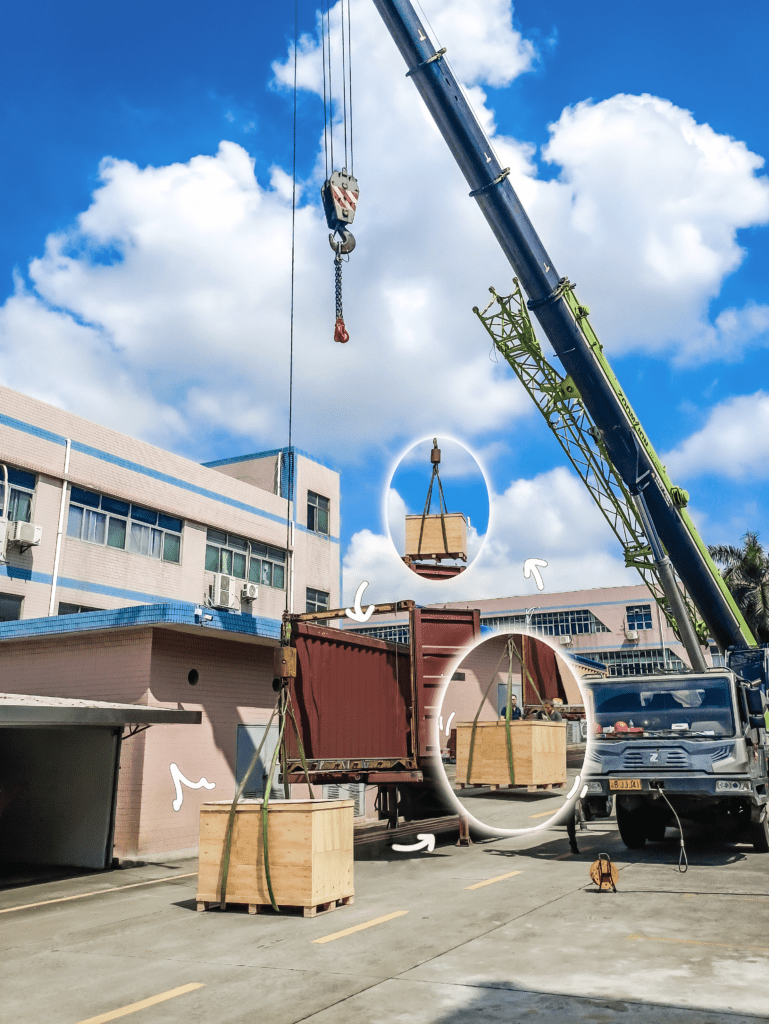
- Once the tool is validated and approved, we prepare it for Tool Shipment. This process includes:
- Packaging: Securely packaging the tool to prevent damage during transportation.
- Logistics: Coordinating with reliable shipping partners to ensure timely delivery.
- Support: Offering post-shipment support to assist with tool installation and initial production setup.