Multi Component Injection Molding
If You Need World-Leading Multi Component Injection Molding, Make Sure You Contact Us!
At HH Plastics, we are a world-leading provider of multi component injection molding, offering cutting-edge manufacturing facilities where we produce complex, high-performance plastic parts with multiple materials or colors.
Our stellar reputation built over time is why many blue-chip brands trust us to deliver maximum product quality while minimising waste and costs. Using our expertise, we perfectly bring their visions to life every time!
Understanding Multi Component Injection Molding
Multi component injection molding (also known as 2K, 3K, or multi-shot molding) is an advanced manufacturing process where two or more different materials or colors are injected into a single mold to create a fully integrated part.
Unlike traditional injection molding—which often requires secondary assembly—multi component molding combines multiple materials in one cycle, reducing production time, labor costs, and potential defects.
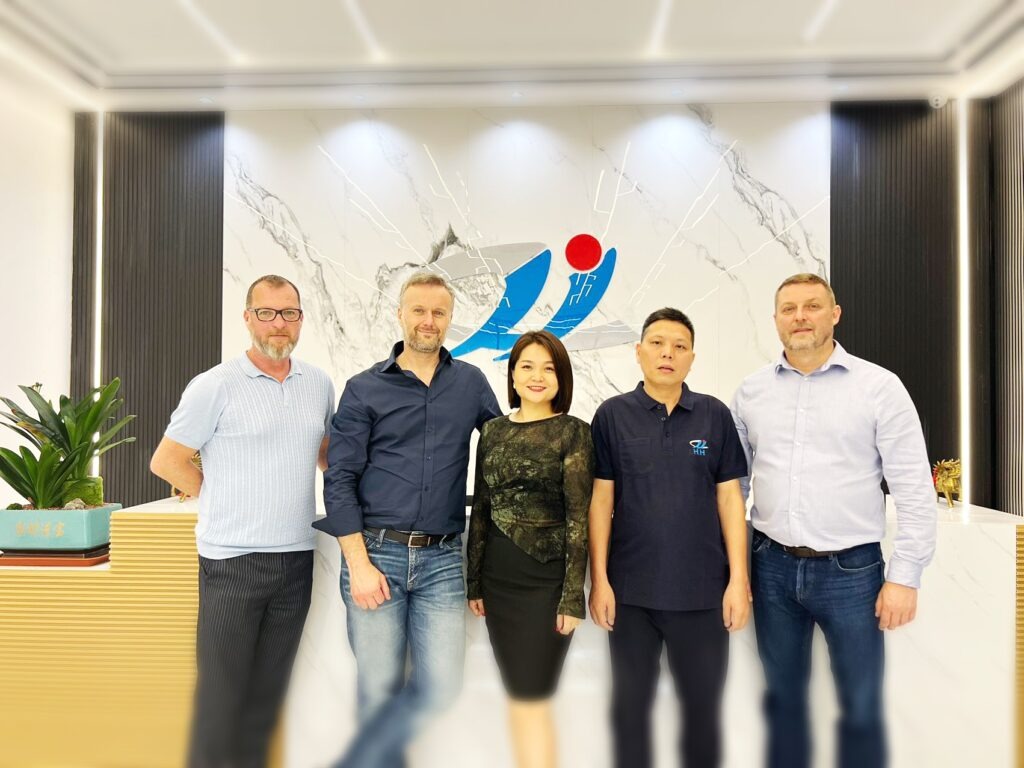
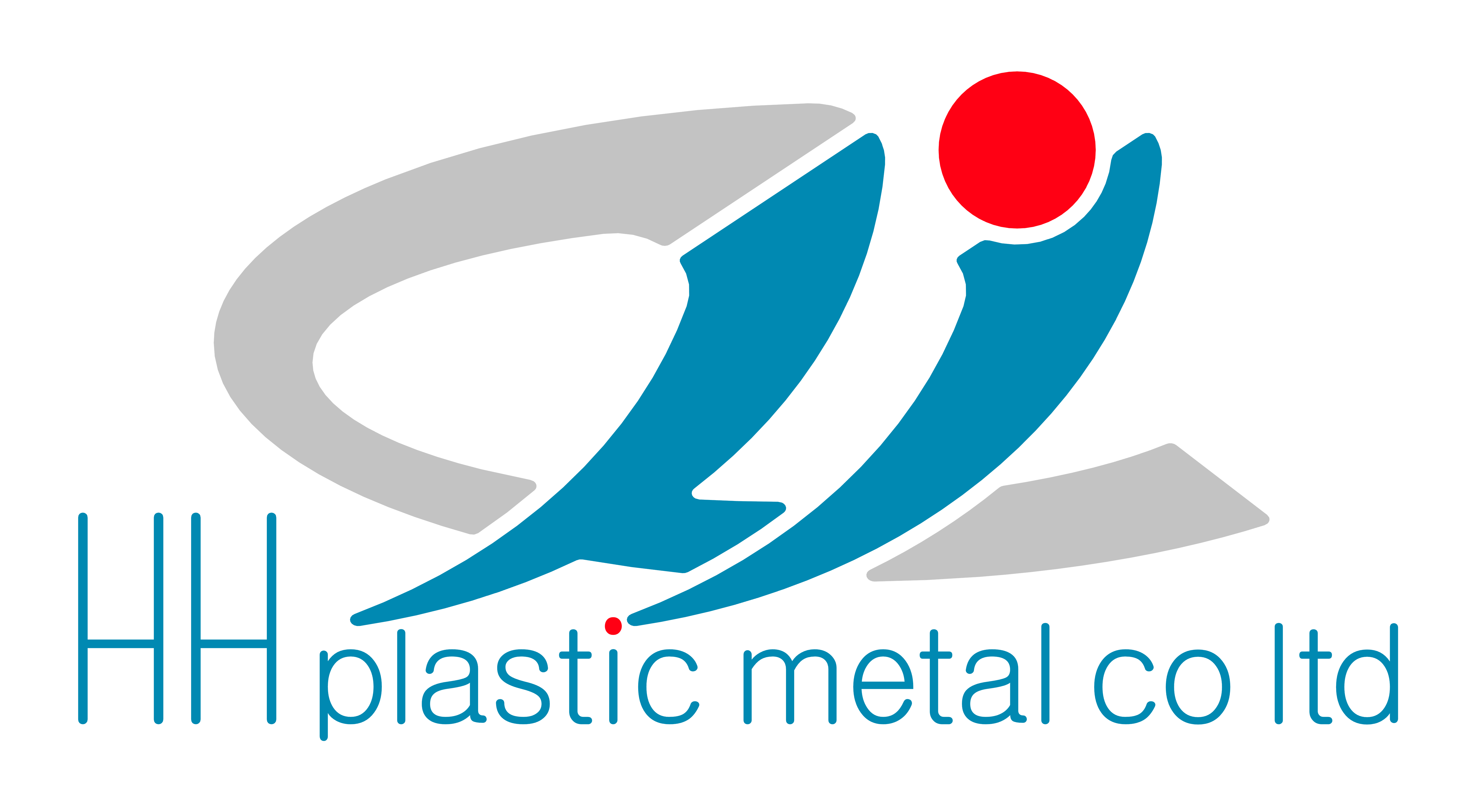
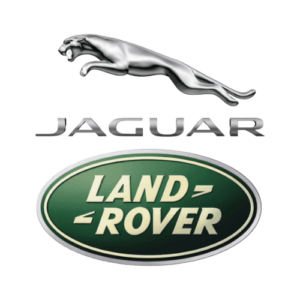
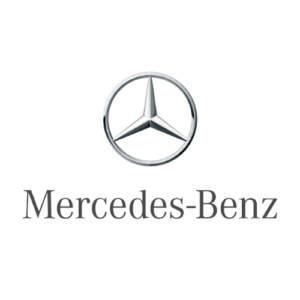
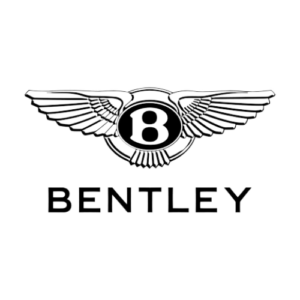
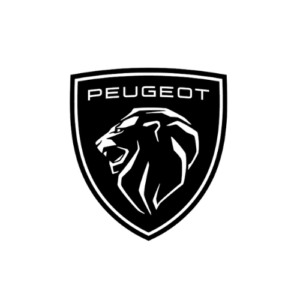
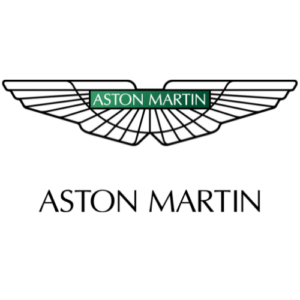
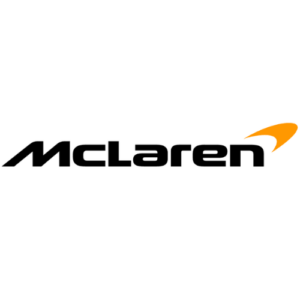
How Multi Component Injection Molding Works
Step 1: First Material Injection – The primary material is injected into the mold cavity.
Step 2: Mold Rotation Or Shuttle Movement – The mold rotates or shifts to position the part for the second injection.
Step 3: Second Material Injection – A different material or color is overmolded onto the first component.
Step 4: Cooling & Ejection – The finished part is cooled and ejected as a single, multi-material component.
This process can be repeated for additional layers, allowing for 3K (three-component) or even 4K molding in highly specialised applications.
The Key Advantages Over Traditional Molding
- Eliminates Unnecessary Steps – No need for glueing, welding, or mechanical fastening.
- Stronger Material Bonding – Chemical or mechanical bonding ensures durability.
- Greater Design Flexibility – Enables complex geometries and hybrid material properties.
- Cost And Time Savings – Reduces labor, logistics, and production waste.
At HH Plastics, we use state-of-the-art multi component injection molding machines and precision tooling to ensure high repeatability, tight tolerances, and superior product quality.
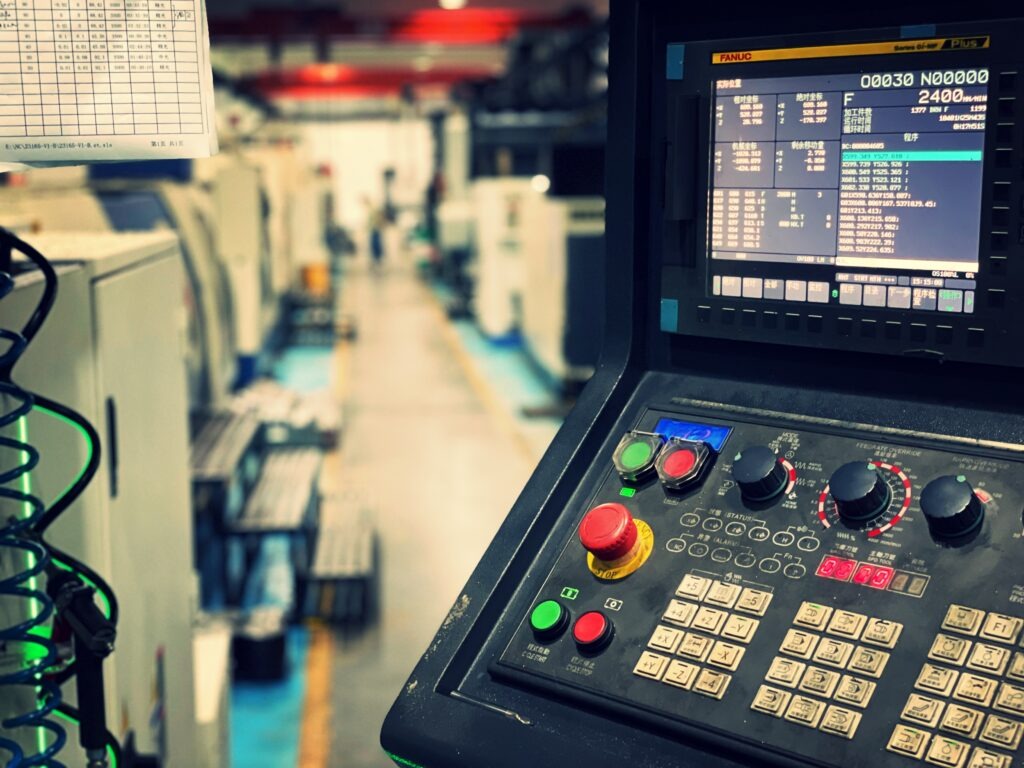
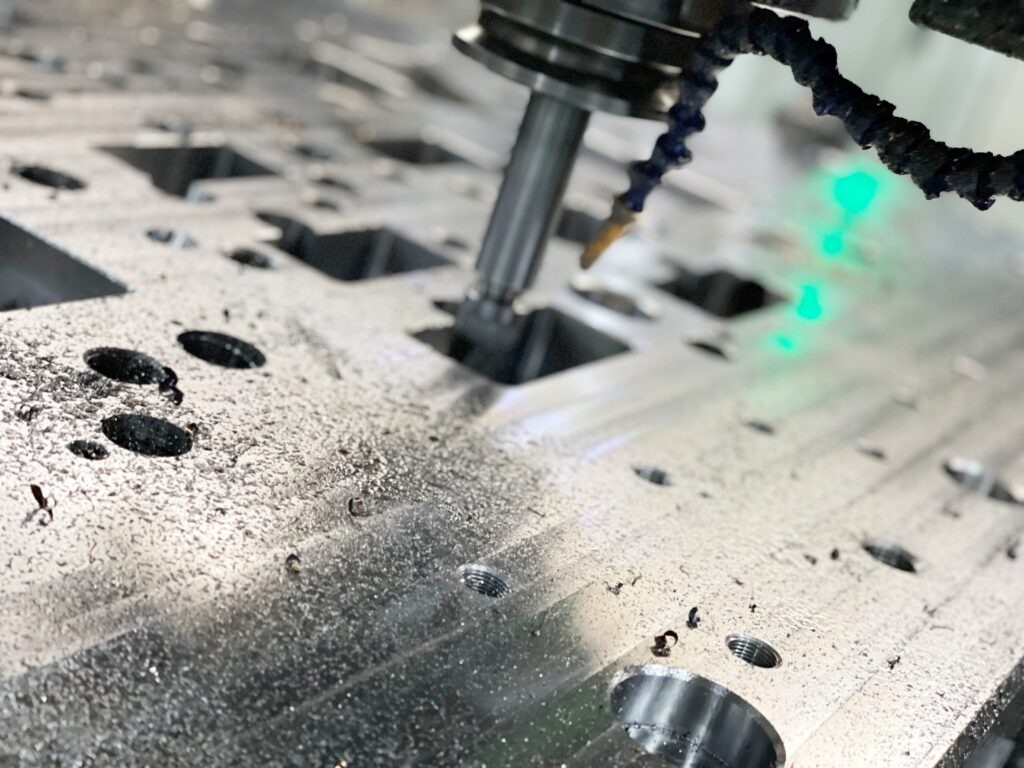
Our mission is to provide high-quality tooling with meticulous attention to detail.
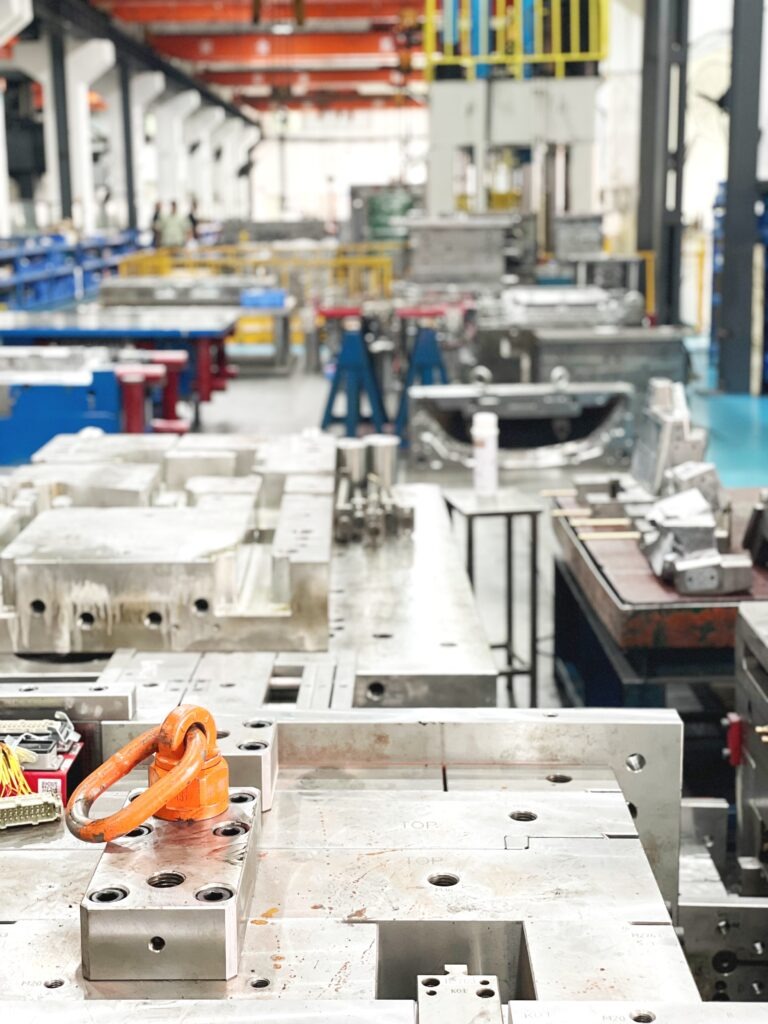
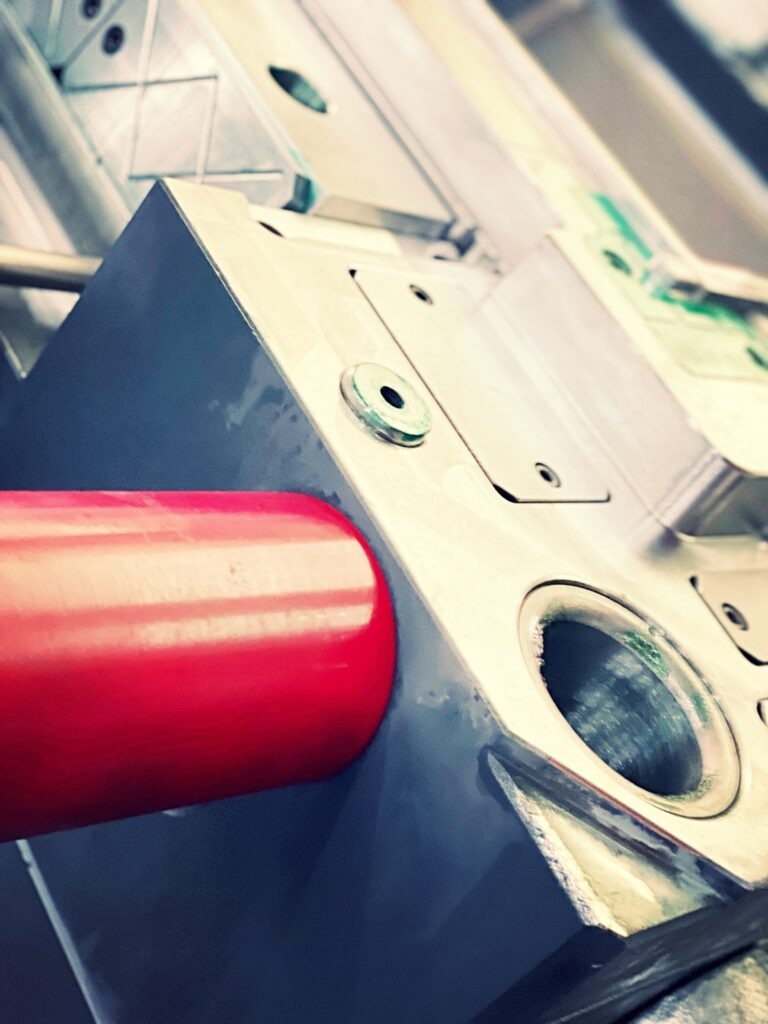
The Key Benefits Of Multi Component Injection Molding
Cost Efficiency And Reduced Production Time
Traditional manufacturing often requires multiple molding cycles and manual assembly, increasing costs and lead times. Multi component molding combines these processes into a single cycle, significantly reducing:
- Labor costs (no secondary assembly required)
- Material waste (less scrap compared to separate molding)
- Logistics and handling (fewer production steps mean fewer opportunities for errors)
Enhanced Product Performance And Durability
By combining different materials, manufacturers can achieve improved functionality that would be impossible with single-material parts. Examples include:
- Soft-touch grips (e.g., TPE overmolded on rigid plastic for tools or medical devices)
- Waterproof seals (e.g., overmolded gaskets for automotive or electronic housings)
- Impact resistance (e.g., shock-absorbing layers in protective cases)
Design Innovation And Aesthetic Flexibility
Multi component molding allows for:
- Multi-color branding (e.g., logos, indicators, or decorative elements molded in one step)
- Living hinges (flexible joints molded directly into rigid parts)
- Integrated seals and gaskets (eliminating the need for separate rubber components)
Stronger, More Reliable Material Bonding
Unlike glued or mechanically fastened parts, multi component molding creates a permanent bond between materials, preventing:
- Delamination (peeling or separation over time)
- Weak spots (common in manually assembled parts)
- Leakage (critical for medical and automotive sealing applications)
Sustainability And Waste Reduction
By minimising secondary processes, multi component molding supports eco-friendly manufacturing through:
- Less material waste (no excess from trimming or assembly)
- Lower energy consumption (fewer production steps mean reduced carbon footprint)
- Longer-lasting products (stronger bonds mean fewer replacements)
The Industry Applications Of Multi Component Molding
We serve a wide range of sectors with our custom multi component solutions, including:
Automotive Industry
- Seals and gaskets (TPE overmolded onto rigid plastic for airtight sealing)
- Dashboard components (soft-touch surfaces integrated with structural parts)
- Multi-color lighting (lenses with integrated light guides)
- HVAC components (vibration-dampening mounts)
Medical And Healthcare Devices
- Ergonomic syringe grips (soft TPE for better handling)
- Sealed enclosures (liquid-resistant housings for diagnostic equipment)
- Wearable devices (flexible, skin-contact sensors overmolded onto rigid frames)
Consumer Electronics And Appliances
- Smartphone and tablet cases (rigid frames with shock-absorbing edges)
- Waterproof connectors (overmolded seals for cables and ports)
- Button pads and controls (tactile silicone keys on plastic substrates)
Industrial And Household Products
- Tool handles (non-slip grips molded onto hard plastic)
- Appliance knobs & seals (integrated for durability)
- Packaging solutions (hinged containers with built-in seals)
Aerospace And Defence
- Vibration-resistant components (multi-material dampening systems)
- Sealed housings (for sensitive electronics in harsh environments)
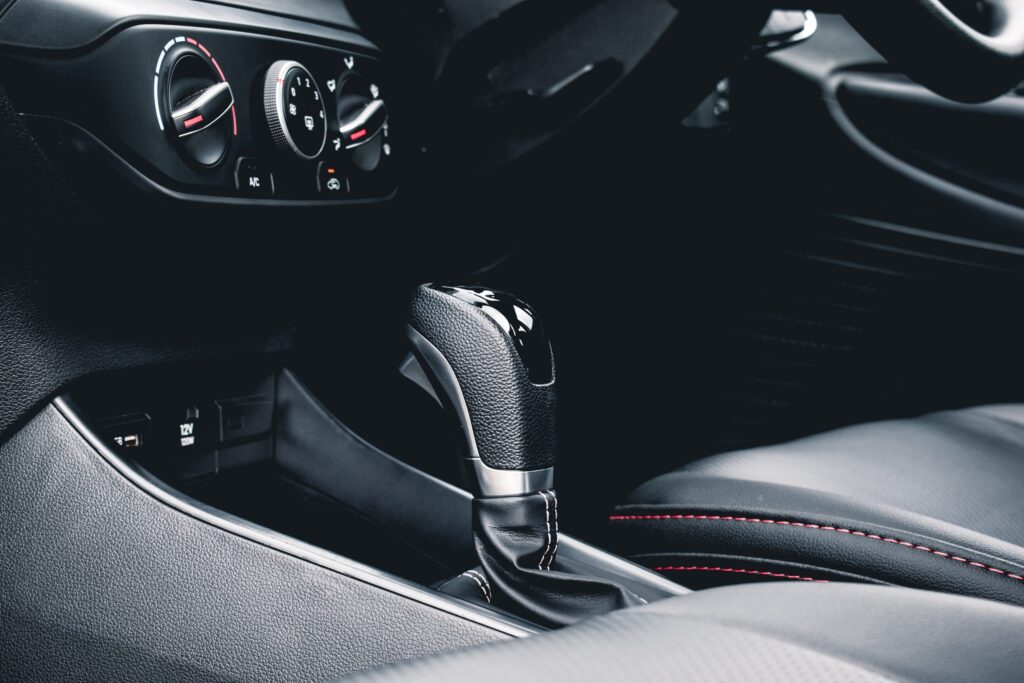
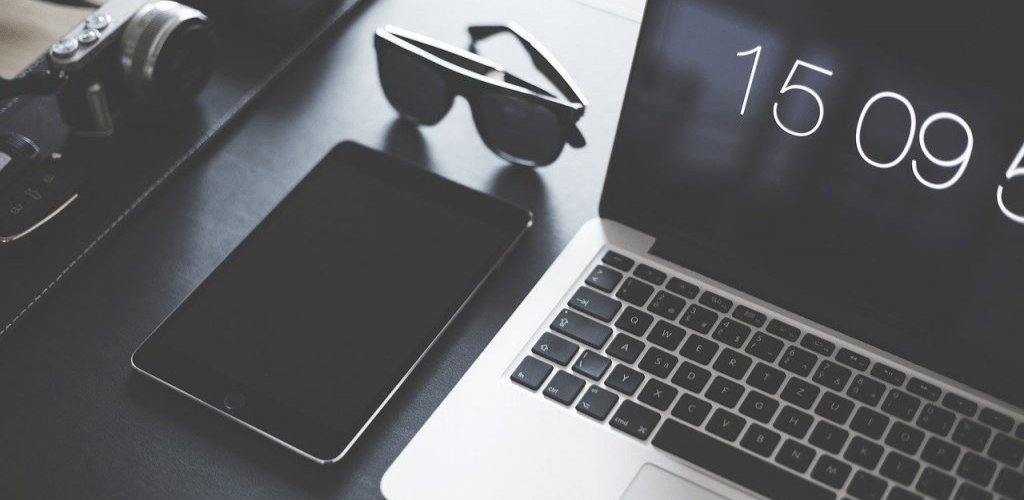
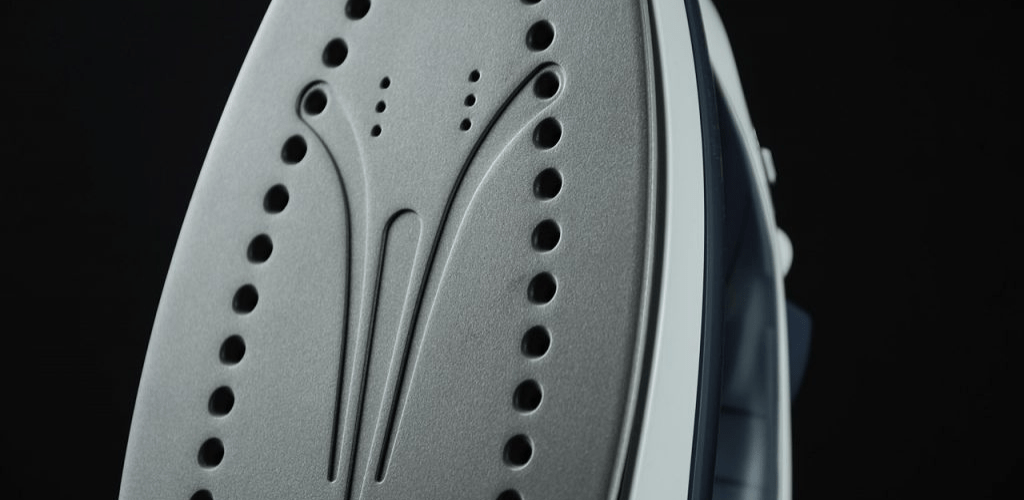
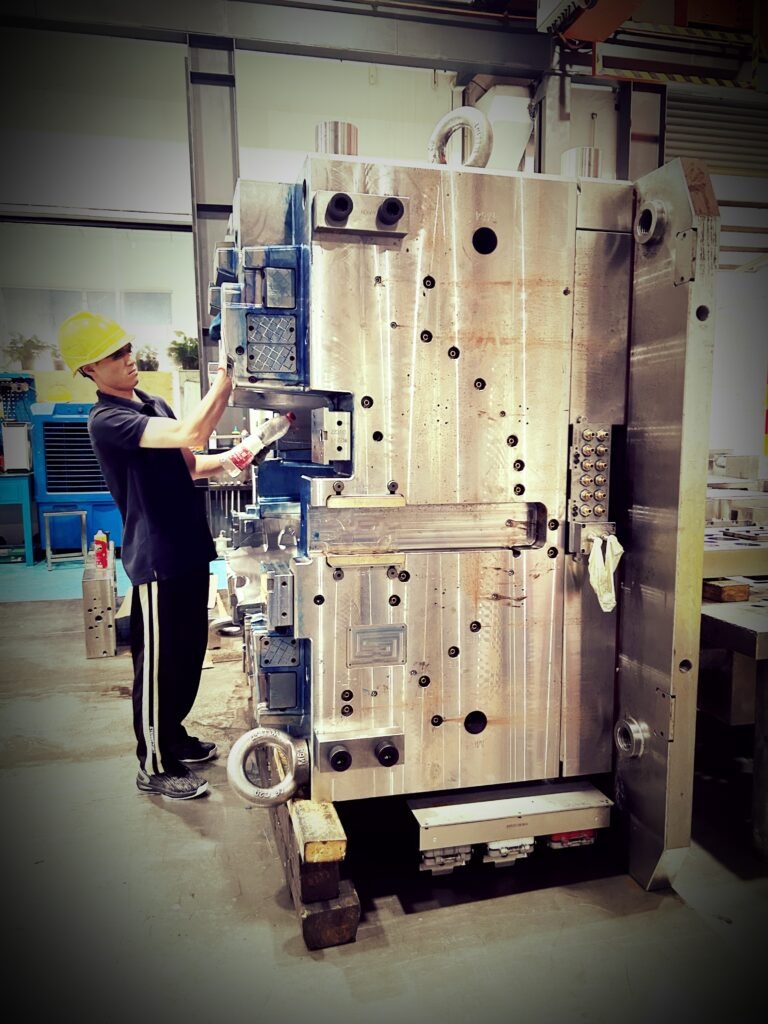
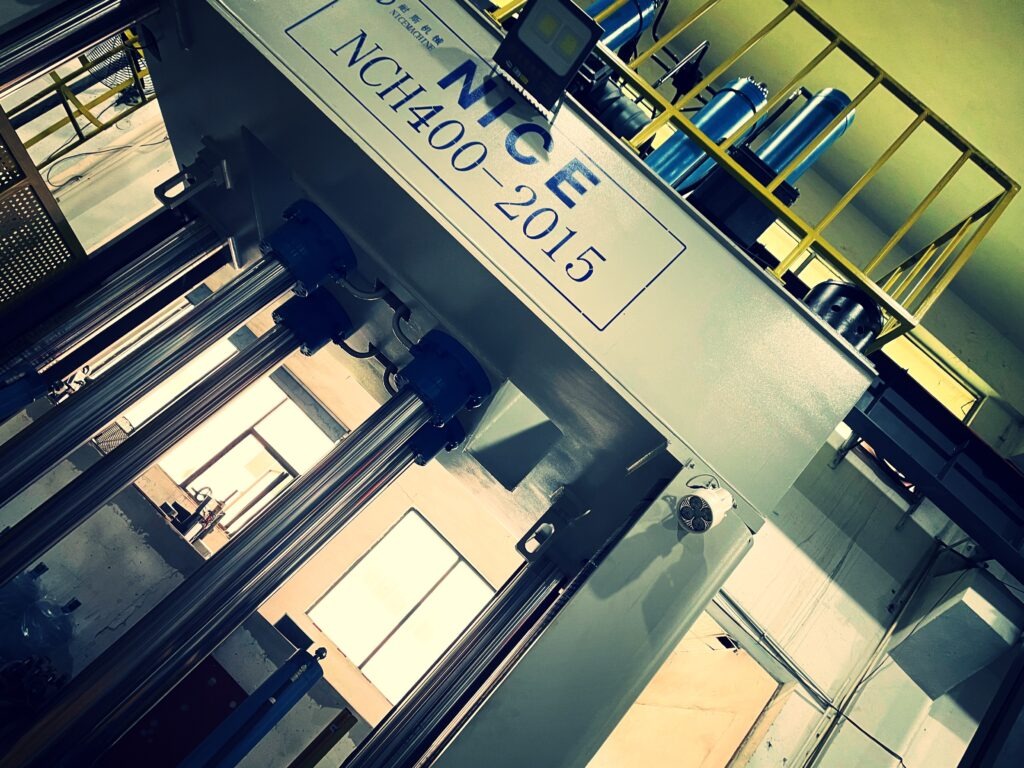
Why Choose Our Multi Component Molding Services?
Our multi component molding services combine advanced machinery, engineering expertise, and rigorous quality control to deliver high-performance multi component parts.
Here is just some of what we can offer:
Cutting-Edge Technology And Equipment
- Multi-shot injection molding machines (for sequential or simultaneous injection)
- Rotary plate and shuttle mold systems (for precise material layering)
- Robotic automation (for consistent part handling and defect reduction)
Material Expertise And Compatibility
We work with a wide range of thermoplastics, elastomers, and engineering resins, including:
- Rigid plastics (PP, ABS, PC, Nylon)
- Flexible materials (TPE, TPU, Silicone)
- High-performance resins (PEEK, PPS for extreme conditions)
Precision Tooling And Design Support
Our team provides:
- Design for manufacturability (DFM) Analysis (optimising part design for cost and performance)
- Prototyping and testing (ensuring material compatibility and functionality)
- High-precision molds (for complex geometries and tight tolerances)
Quality Assurance And Industry Compliance
- ISO-certified production processes
- In-house testing (dimensional checks, tensile strength, material bonding tests)
- Full compliance with industry standards (including automotive, medical, food-grade, and aerospace)
Why Choose HH Plastics?
Whether you need multi-material, multicolor, or overmolded components, our highly skilled team at HH Plastics has the technology, expertise, and manufacturing excellence to bring your designs to life. The benefits of using our multi component injection molding services include:
- Superior Product Quality (seamless material bonding, high durability)
- End-To-End Support (from concept design to full-scale production)
- Custom Solutions (tailored to your industry and application needs)
- Cost-Efficient Manufacturing (reduced assembly = lower costs)
- Decades Of Experience in complex injection molding solutions
And our multi component injection molding services help you:
- Improve Product Performance (enhanced functionality & durability)
- Accelerate Time-To-Market (streamlined manufacturing process)
- Reduce Production Costs (fewer assembly steps, less waste)
Contact us today to discuss your project requirements and discover how our multi component molding solutions can benefit your business!
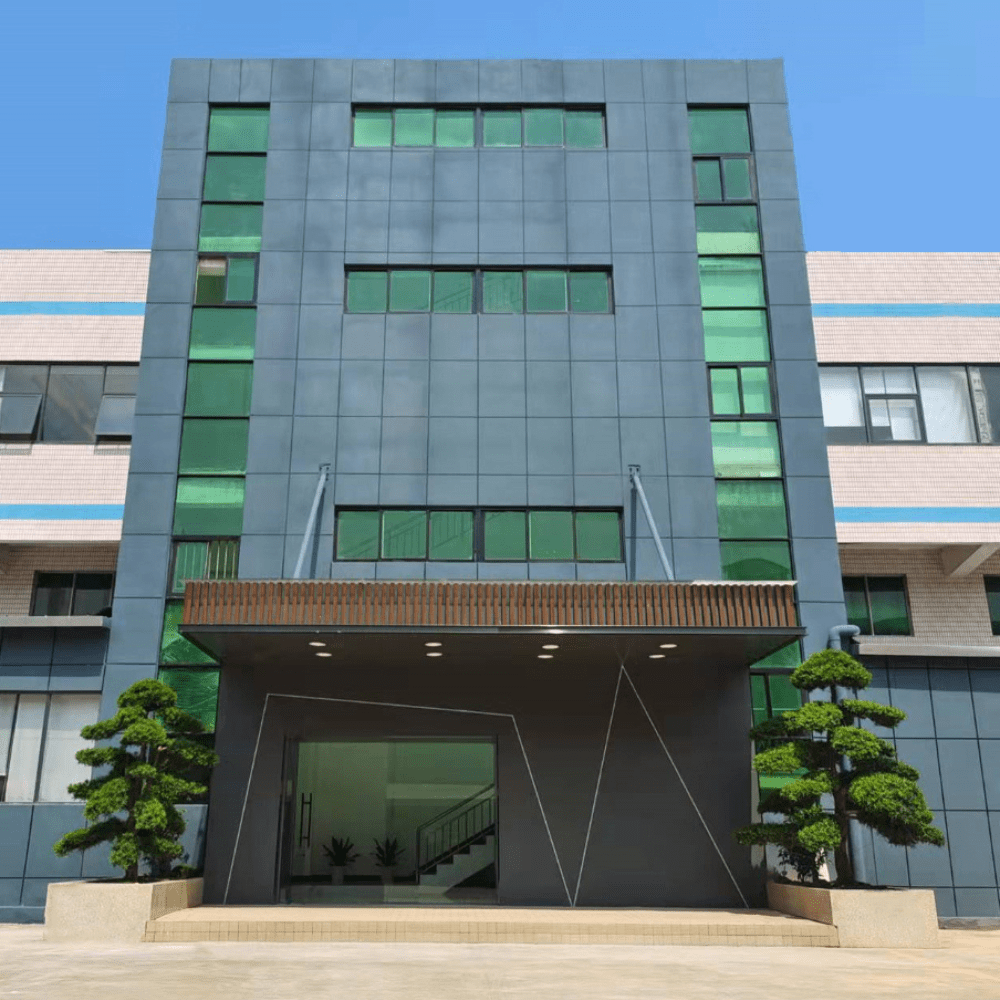