Twin Shot Injection Moulding
We Provide Top-Quality Twin Shot Injection Moulding
At HH Plastics, we offer expert twin shot injection moulding services for a wide range of industries. Our process allows manufacturers to integrate two distinct materials into a single moulded part, creating components that are both highly functional and visually appealing.
By combining our extensive experience with a commitment to technological innovation, we have established ourselves as a valuable partner for world-leading clients in sectors such as automotive, consumer electronics, aerospace, home appliances, and more.
Understanding Twin Shot Injection Moulding
Twin shot injection moulding is an advanced manufacturing process where two different materials are injected into a single mould, typically in two stages.
In the first stage, the base material forms the initial part, which is then transferred to another cavity or rotated within the mould for the second material to be injected. This allows for the combination of materials with varying properties, such as rigidity and flexibility, or the use of multiple colours and textures in a single component.
Twin shot injection moulding offers several advantages over traditional moulding techniques, especially in industries requiring parts with multiple functions. For example, automotive manufacturers often need components that combine a hard, durable structure with a soft-touch surface, such as steering wheel grips or dashboard buttons.
Similarly, in consumer electronics, the ability to combine different materials and finishes within one component allows for the production of ergonomic and visually appealing devices.
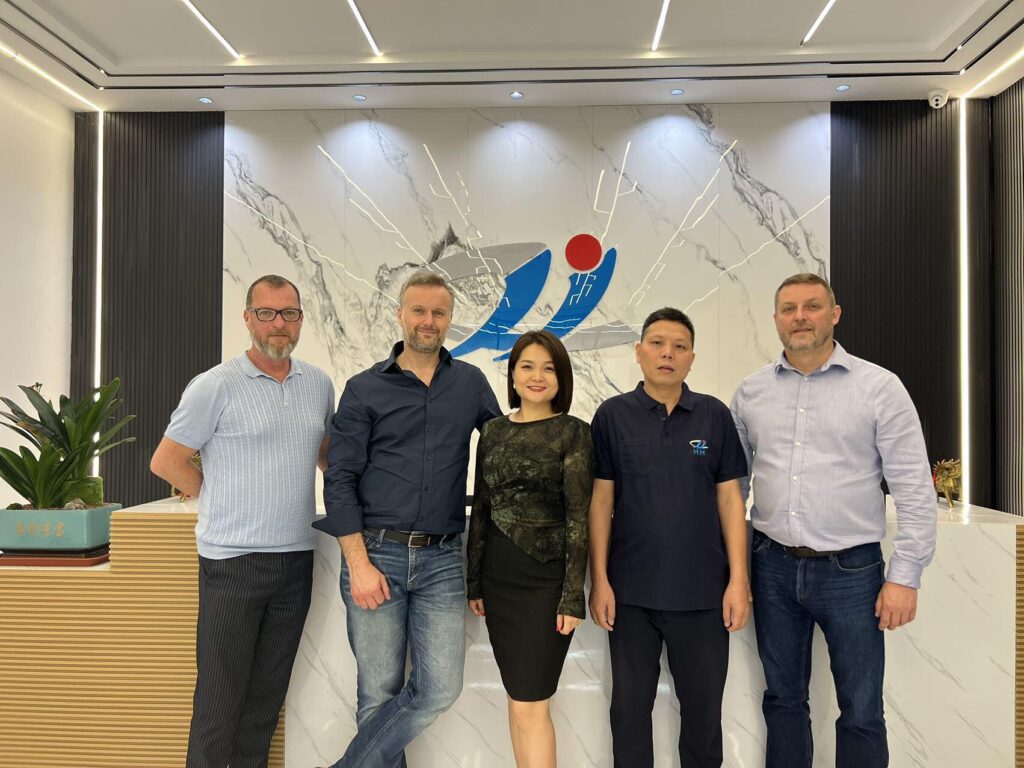
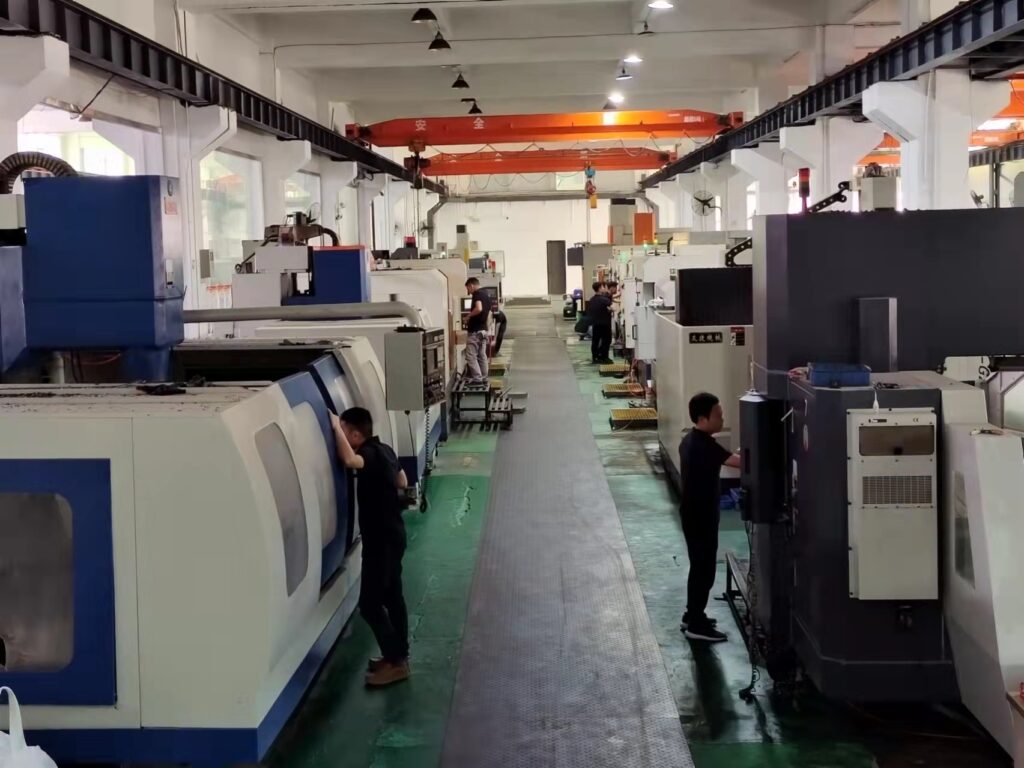
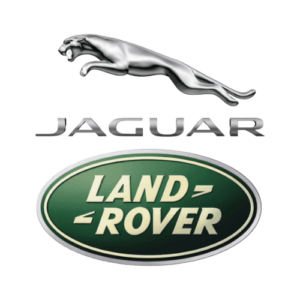
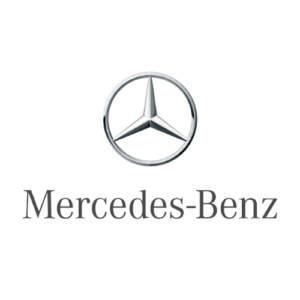
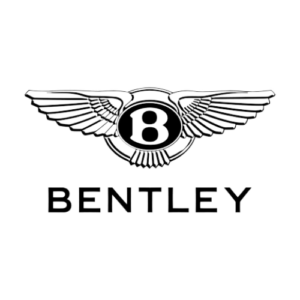
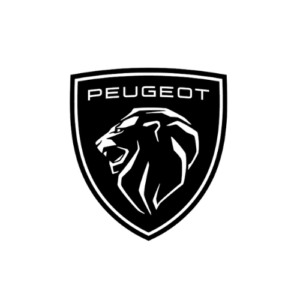
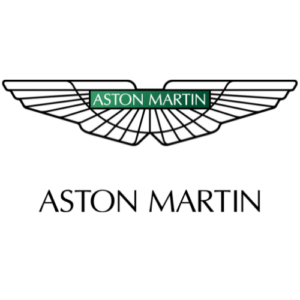
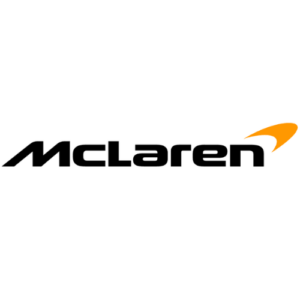
How We Can Help
Our decades of expertise in the injection moulding field have equipped our team with a deep understanding of the complexities of twin shot moulding.
Our highly skilled professionals are proficient in managing the nuances of this intricate process, ensuring each project is executed with meticulous attention to detail. From the initial material selection to designing moulds that account for the thermal and chemical properties of each component, we ensure each product we design meets the specific demands of each industry.
This extensive experience allows us to serve a diverse range of sectors, supporting them to overcome their unique challenges and requirements. Plus, we are equipped to handle the most stringent of design specifications, creating products that are durable, functional and visually appealing.
Cutting-Edge Technology For Precise Manufacturing
At HH Plastics, we are proud to invest in cutting-edge technology, ensuring that we remain at the forefront of twin shot injection moulding services.
Using state-of-the-art equipment, we are capable of handling complex projects that require extreme accuracy and repeatability. This level of precision is particularly important for producing parts with intricate designs or tight tolerances, such as those found in high-end consumer electronics or automotive applications.
Our high-end technology allows for greater control over the moulding process, ensuring perfect alignment of the materials and seamless bonding between them. This high level of control means that each part we produce meets exacting specifications, often required in industries where even the slightest defect could lead to product failure.
In addition, our commitment to harnessing the latest in injection moulding technology gives us a significant competitive advantage, enabling us to deliver consistent quality over high or low production volumes.
Bespoke Solutions, Whatever Your Sector
Our team at HH Plastics recognises that no two clients – or their projects – are the same. Each industry has its unique set of challenges and requirements, which is why we take a bespoke approach to every project.
Whether you need a high-volume production run for automotive components or a smaller, more specialised batch for consumer electronics, we can offer a tailored solution to meet your needs.
Our customisation process begins with close collaboration with clients, ensuring that every aspect of the design, material selection, and production is suitable for the final product’s intended use.
For example, in the home appliances sector, a product might need to combine durability with aesthetic appeal, such as a refrigerator handle that is strong enough to withstand repeated use but also comfortable and visually pleasing.
Our ability to combine different materials in one mould makes twin shot injection moulding ideal for such applications, and our comprehensive solutions ensure that clients receive components that meet both functional and aesthetic requirements.
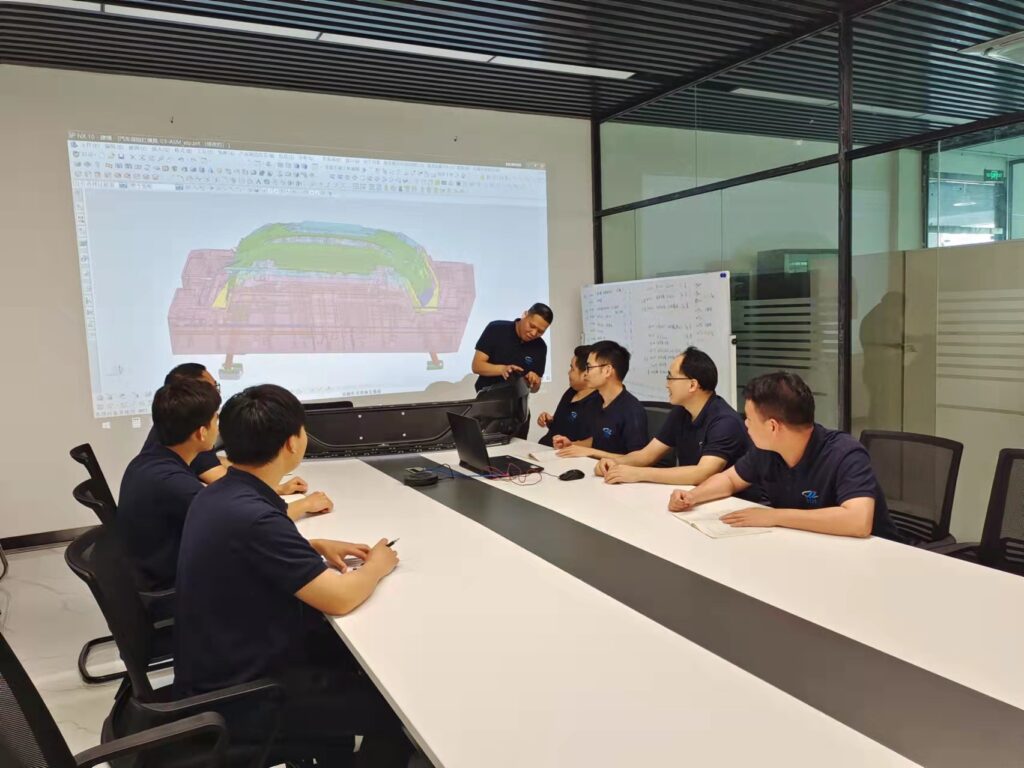
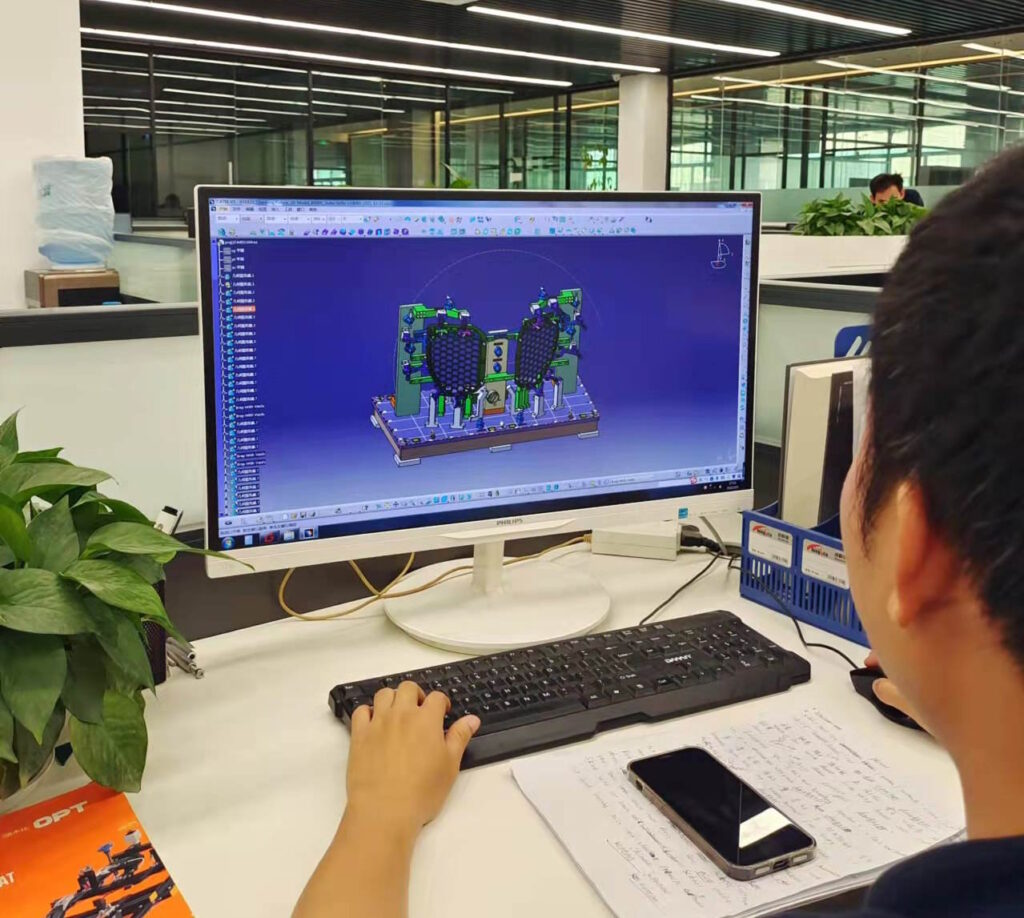
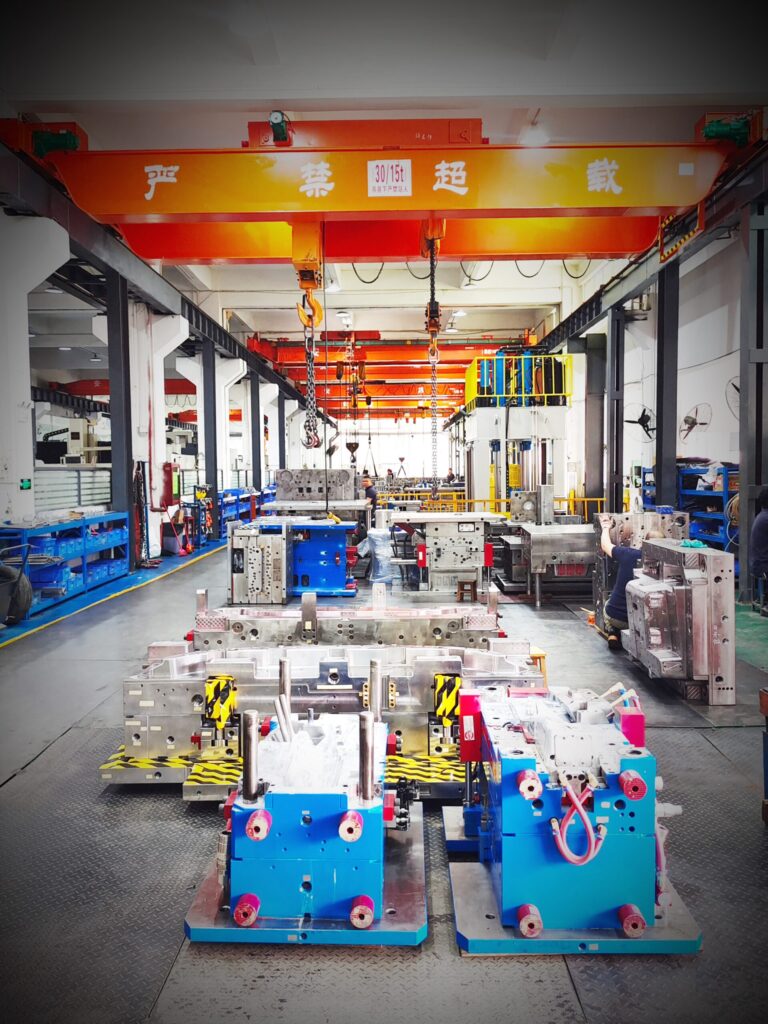
Our mission is to provide high-quality tooling with meticulous attention to detail.
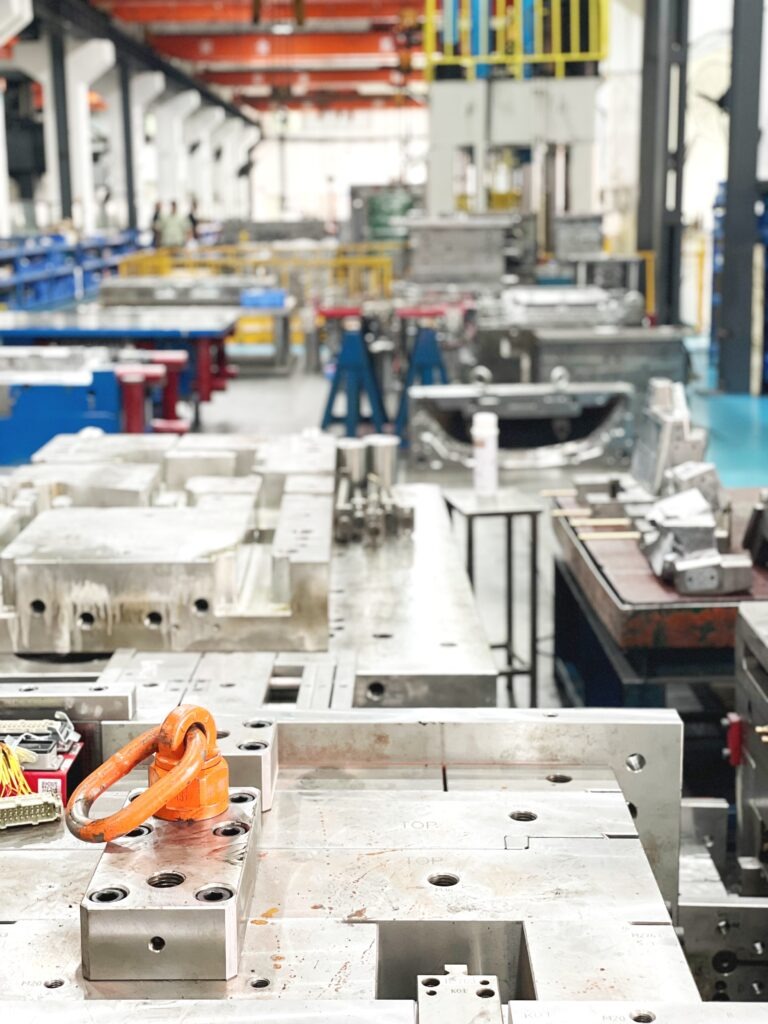
The Benefits Of Twin Shot Injection Moulding
Enhanced Product Functionality And Design
Twin shot injection moulding allows for the creation of parts that offer enhanced functionality and design by combining materials with different properties.
This is particularly significant in industries such as automotive, where a single component may need to combine strength and flexibility, or hardness and softness. For example, a car’s dashboard controls might have a rigid, durable base but require a soft, tactile finish for user comfort.
Meanwhile, in the consumer electronics sector, design plays a critical factor in product success. Here, twin shot moulding enables the integration of different colours and textures into a single component, allowing manufacturers to create sleek, modern devices that are both functional and visually appealing.
The ability to combine different materials also enhances the ergonomic qualities of products, making them more comfortable to use without compromising on strength or durability.
One of the most significant advantages of twin shot injection moulding is its efficiency.
By integrating two materials in a single moulding cycle, secondary processes such as overmoulding or assembling separate parts can be eliminated, reducing both production times and costs. This is particularly beneficial for companies involved in high-volume production, as the streamlined process leads to quicker turnaround times and lower labour costs.
Twin shot moulding also offers time and cost savings to companies which require smaller production runs, as the process ensures greater consistency and quality in the finished parts.
At HH Plastics, we harness this efficiency, enabling us to deliver cost-effective solutions to clients, whether they require high-volume production or smaller manufacturing runs.
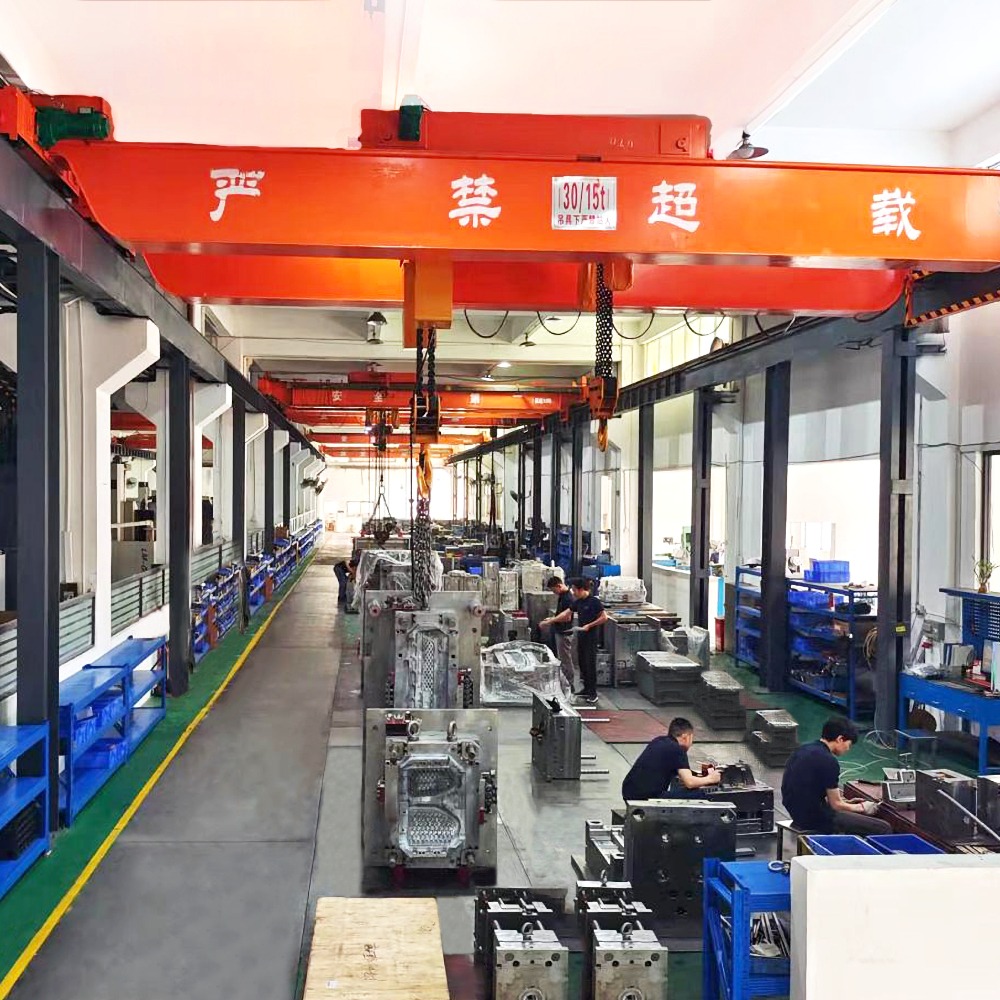
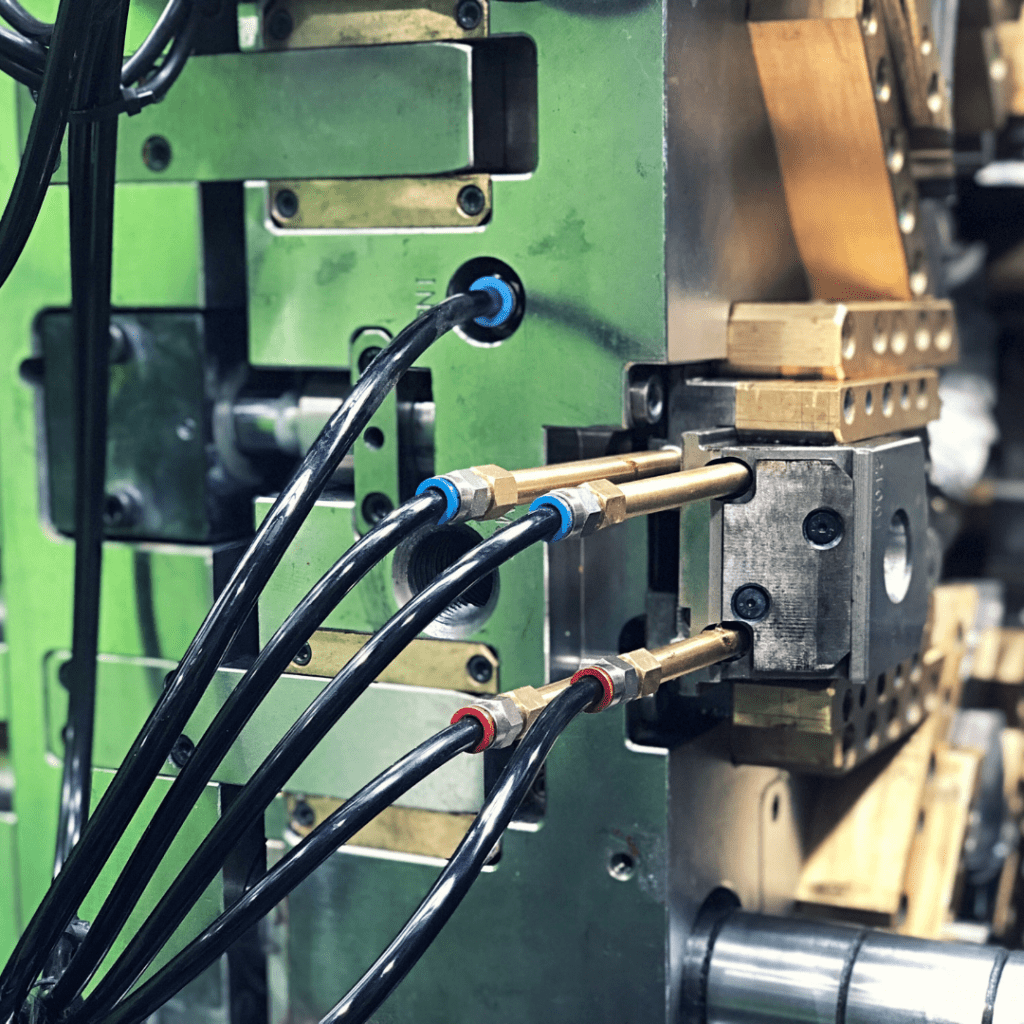
Improved Durability And Strength
Components produced using twin shot injection moulding are often more durable than those assembled from multiple parts.
This is because the bonding of materials during the moulding process creates a more unified and structurally sound component. The result is a part that is better able to withstand stress, wear and tear, and exposure to the elements, making it ideal for industries where durability is essential.
For example, in the automotive industry, components like steering wheel grips or door handles are subject to frequent use and need to remain functional over long periods. Twin shot injection moulding allows for the integration of materials that not only improve the comfort and ergonomics of these parts but also enhance their strength and longevity.
The process can also be used to improve resistance to chemicals, heat, or impact, further extending the lifespan of the product.
Twin shot injection moulding is suitable for a wide variety of designs, especially for products where appearance is as important as functionality.
The ability to combine different colours, textures, and finishes within a single component allows manufacturers to create products that are both visually appealing and functional. This is particularly valuable in consumer-facing industries such as electronics, where product aesthetics play a significant role in consumer purchasing decisions.
In short, twin shot moulding offers manufacturers a level of design versatility that is difficult to achieve with traditional moulding processes. This aesthetic flexibility ensures that products not only perform well but also stand out in competitive markets.
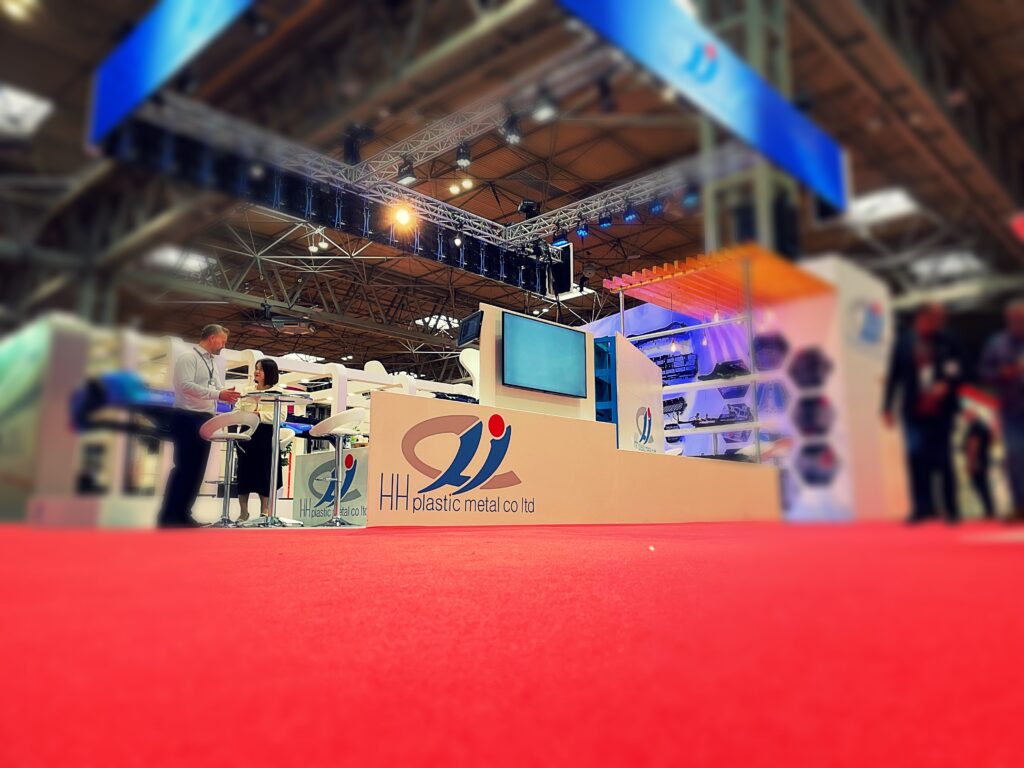
HH Plastics: Committed To Innovation And Sustainability
At HH Plastics, we prioritise innovation and sustainability. We continually invest in new technologies and processes to enhance our twin shot injection moulding services, ensuring that clients benefit from the most advanced manufacturing solutions on the market.
Our commitment to innovation is complimented by our sustainable approach, adopting environmentally friendly practices such as minimising material waste and optimising energy use during production.
As sustainability becomes increasingly important across industries, our core principles ensure that our client base receives not only high-quality products but also solutions that reduce environmental impact.
This dual focus on innovation and sustainability positions us as a trusted partner for businesses looking to meet their production goals while adhering to environmentally responsible practices.
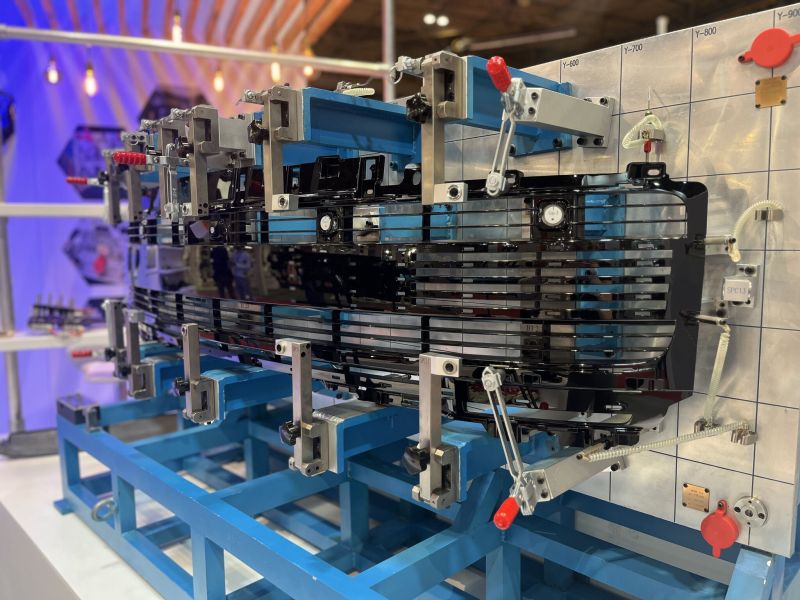