Die Casting and Stamp Tooling
Die Casting and Stamping
Tooling
The instruments that form and cut sheet metal pieces are known as stamping dies. To build and prove-out highly precise, unambiguous designs, they are often developed utilising computer-aided design (CAD) software and analytical applications. Skilled craftspeople called as diemakers then translate these designs into stamping dies.
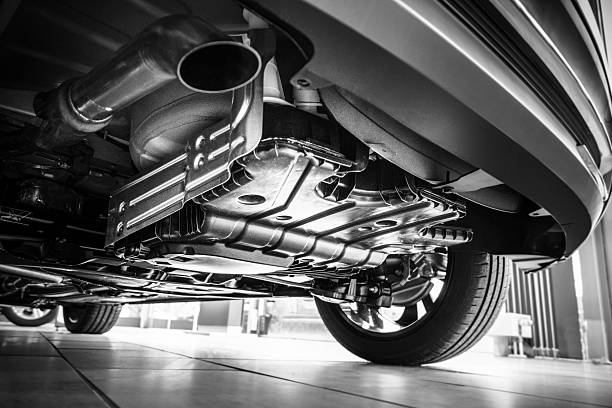
Our mission is to provide high-quality tooling with meticulous attention to detail.
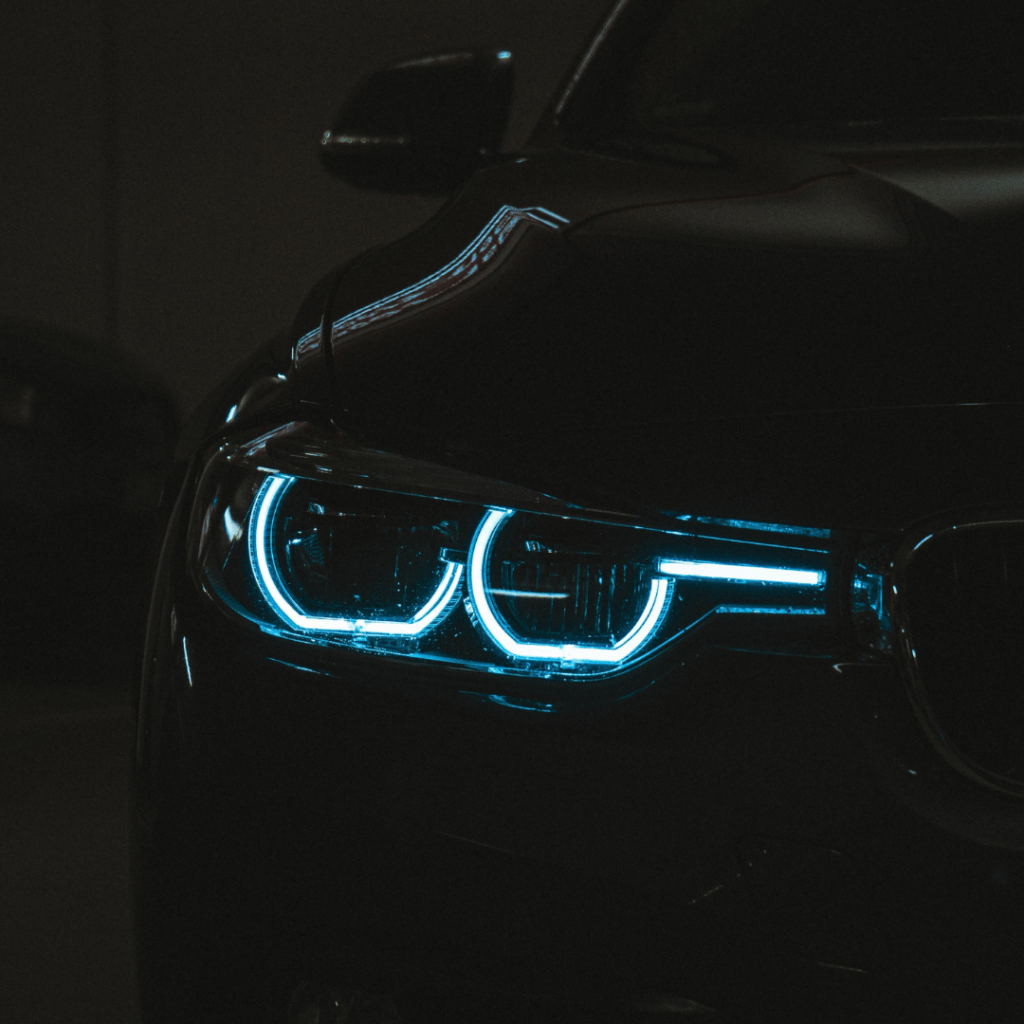
We work together with you at HH Plastic Metal Co., Ltd to design and develop die casts that completely match your application needs. We sell parts to a wide range of sectors as a trusted name and leading technical component manufacturer. Our customers in the automotive, medical, home appliances, and electronics industries benefit from high-quality parts at low prices. For you, having a lot of manufacturing experience means more specialisation options, higher production rates, and better component performance. You may rest assured that you will always get consistent great quality and good value for your money.
We can develop 2D toloerance drawings and 3D models, analyse for accuracy, add assembly features, draught angles, tool finish, and more for customers that don’t have comprehensive design expertise. Our castings provide the finest performance and comply to your required tolerances at the component level. Die Fill, Mechanical Performance, and Casting Ease are the top three design concerns that help us achieve the highest quality standards. We can help you eliminate cold welds, air pockets, and cold casting by conducting a detailed study in these regions. We may also make sure that any Finite Element Analysis (FEA) for mechanical strength isn’t thrown off by unknown casting faults.
We can tailor our services to provide the exact finish you require for your product at HH Plastic Metal Co., Ltd. Your parts can be cast, trimmed, pre-machined, fully machined, or with surface finish, among other possibilities. Some of the techniques we use to change the finish post cast include shot blasting, bead blasting, and vibratory tumbling. Powder coating, painting, anodizing, and plating are some of the high-quality surface finishes we can provide. For improved reproducibility, we do all of our post-casting with CNC machining.
A Progressive stamping die is a one-of-a-kind precise instrument for cutting and shaping sheet metal into a specific shape or profile. The die’s cutting and forming parts are usually made of tool steel, which is a type of hardenable steel. Cutting and shaping portions composed of carbide or other hard, wear-resistant materials can also be found in dies. Here at HH Plastic Metal Co., Ltd, we manufacture a variety of high-speed stamping dies, all of which execute one of two basic operations: cutting, shaping, or both. Line dies are dies that are manually or robotically loaded. Automated progressive and transfer dies are available. Progressive dies are designed to function at high speeds and are employed in higher-volume production. Here at HH we create progressive dies that are high-quality, dependable, and cost-effective for the automotive, appliance, consumer electronics, and aerospace industries.
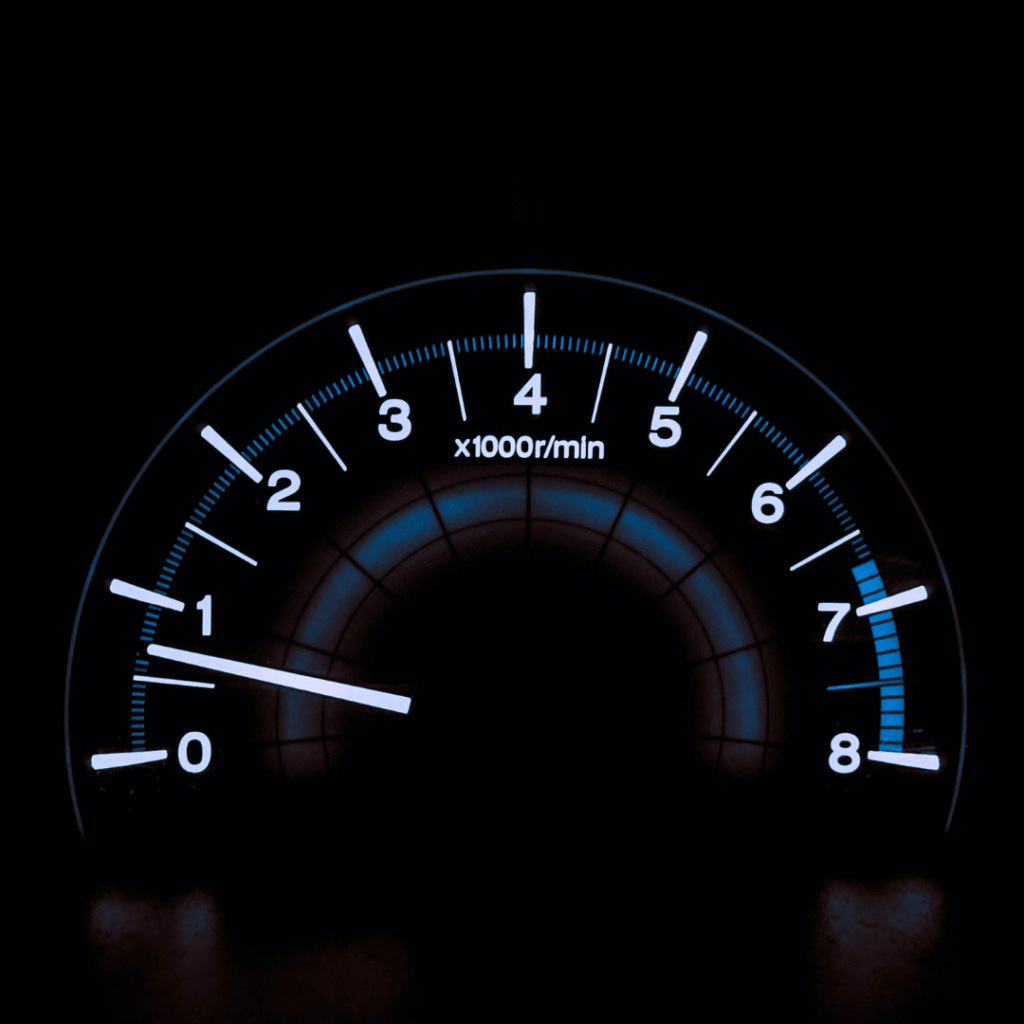
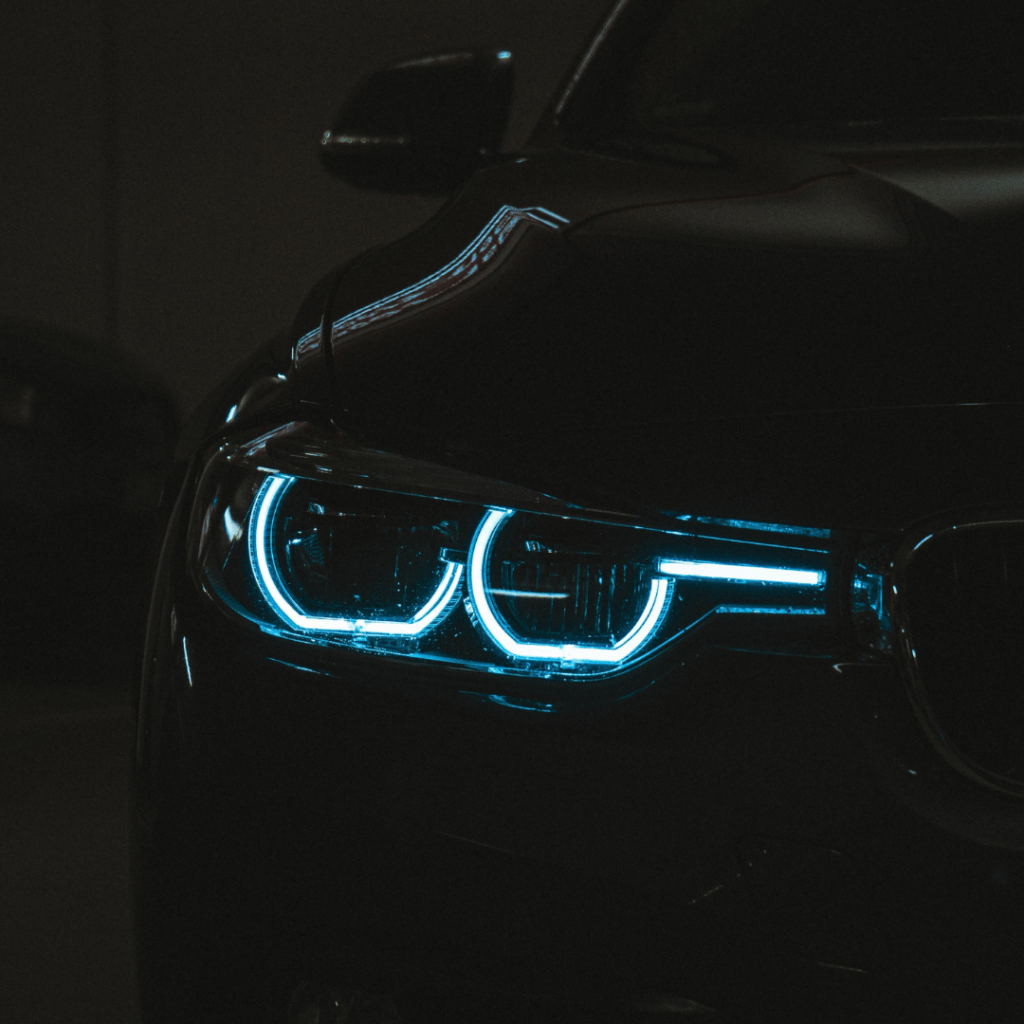
At HH Plastics, we think that having a single point of contact within the Project Management team benefits clients and facilitates communication. Regular internal meetings guarantee that we are all on the same page and that we produce high-quality solutions as a team. Our talented and devoted team is dedicated to exceeding customer expectations. Experienced employees with extensive experience of creating moulds for a wide range of industries ensure efficient, high-quality design, management, and manufacturing solutions.
Our goal is to exceed our clients’ expectations by providing well-built tools and providing outstanding management and delivery services in order to fulfil their high performance criteria. We feel that this is the most effective strategy to secure long-term success and connections.
At HH, we think that having a robust process-driven management system in place is critical to reliably producing high-quality moulds on time, every time. We think that the quality of our moulds, as well as our ability to demonstrate a high level of project management, is the foundation for our clients’ continuous long-term support.